Интегрированное проектирование и инженерные расчеты помогают НАСА в создании ракетоносителя нового поколения
<p >Кинематический и КЭ-анализ в Simcenter 3D, а также использование Teamcenter для управления интегрированным процессом помогло инженерам убедиться в том, что сопло большего размера не ударится о стартовый комплекс при пуске.</p>
Группа компаний ATK Aerospace
Группа компаний ATK Aerospace – основной мировой производитель твердотопливных ракетных двигателей и ведущий поставщик комплектующих для военных и гражданских самолетов.
https://www.orbitalatk.com/- Штаб-квартира:
- Brigham City, Utah, United States
- Решения:
- NX, Simcenter 3D Software, Simcenter Nastran, Simcenter Products, Teamcenter
- Отрасль:
- Aerospace & defense
Нас и компанию Siemens связывает многолетнее партнерство.
Группа компаний ATK Aerospace
Пример внедрения: Группа компаний ATK Aerospace
Самая мощная ракета в мире
Группа компаний ATK Aerospace – основной мировой производитель твердотопливных ракетных двигателей и ведущий поставщик комплектующих для военных и гражданских самолетов. Кроме того, компания специализируется на изготовлении малых спутников и микроспутников, узлов и подсистем космических аппаратов, легких орбитальных объектов и солнечных панелей, дешевых и быстрореализуемых решений по выводу полезной нагрузки в космос, а также осветительных ракет и ложных целей, материалов для энергетики и смежных отраслей. Группа компаний обладает обширным опытом по поддержке беспилотных и пилотируемых полетов.
Один из текущих проектов группы ATK – ракетоноситель Space Launch System (SLS), являющийся преемником космических шаттлов. В документах НАСА проект SLS описывается как «крупнейшая и обладающая наибольшими возможностями ракета, предназначенная для нового поколения пилотируемых полетов за пределы околоземной орбиты». SLS станет первой в НАСА ракетой такого класса с того момента, как носитель Saturn V доставил американских астронавтов на Луну свыше 40 лет назад. Однако ракета SLS сможет вывести человека еще дальше в космос, в том числе и в экспедиции на Марс. Первый запуск намечен на 2017 год.
Компания ATK разрабатывает твердотопливные ускорители ракеты SLS – два двигателя по обеим сторонам главной ступени, дающие дополнительную тягу в течение первых двух минут полета. В первых полетах носителя SLS будут применяться модифицированные ускорители от космического челнока, также спроектированные в компании ATK. Однако компания ATK создает и новые ускорители с увеличенной тягой, которые будут применяться в последующих полетах с большей полезной нагрузкой.
Включение процессов инженерного анализа в PLM-среду
Компания АTK уже почти десять лет применяет технологии по управлению жизненным циклом изделия (PLM), разработанные компанией Siemens PLM Software. К ним относятся система автоматизированного проектирования NX™ и система управления процессами и данными об изделии Teamcenter®. «Нас и компанию Siemens связывает многолетнее партнерство, – рассказывает Рамеш Кришнан (Ramesh Krishnan), главный инженер отдела технологических процессов и инструментов компании ATK. – Это сотрудничество началось благодаря дальновидной позиции руководства, которое осознавало всю пользу интегрированной системы».
Последние годы группа компаний работала над углублением интеграции инженерных расчетов в процесс проектирования. «Мы столкнулись с задачей применения процессов инженерного анализа [CAE] на ранних этапах разработки изделия, чтобы конструкция создавалась на основе результатов расчетов, – поясняет Натан Кристенсен (Nathan Christensen), старший руководитель отдела технологических процессов и инструментов компании ATK. – Это очень сложное дело, с учетом специфики нашей работы и высокой сложности применяемых инструментов». Работа по проектированию сопла нового ускорителя в рамках программы SLS – отличный пример того, как эту задачу удалось успешно решить.
«Чтобы повысить характеристики наших двигателей, размер сопла требовалось бы существенно увеличить, – поясняет Кришнан. – При этом в ходе подъема ракеты такое увеличенное сопло может столкнуться со множеством элементов пускового сооружения».
На заднем конце ускорителя имеется коническая секция. Пусковые крепления захватывают эту секцию и удерживают ракету на стартовом столе. Компания ATK впервые в своей практике разрабатывает убираемые крепления, которые при пуске будут отводиться, чтобы не произошло столкновения с соплом.
Инженеры компании ATK в системе NX создали модель задней части ускорителя, включая коническую секцию и механизм отвода креплений. Затем представленная в цифровом виде геометрия применялась для выполнения двух видов расчетов: кинематического и конечно-элементного (КЭ).
Убираемые крепления и ураганный ветер
Компания ATK применила модуль NX Motion с целью моделирования кинематики движений убираемых креплений при пуске ракеты. «Мы задали график изменения скорости ракеты в электронной таблице Excel и затем подключили эту таблицу в качестве источника данных о скорости моделируемого объекта, – рассказывает Кришнан. – Мы использовали зависимость тяги двигателей от времени, что оказалось правильным выбором. По расчетам, ракета запускалась с требуемым ускорением».
«Работавший над этой задачей инженер ранее не имел дела с модулем NX Motion, но он быстро разобрался в нем и уже через несколько дней получил готовую модель», – отмечает Кришнан. Созданная им численная модель учитывала даже четырехдюймовый болт, которым фиксируются пусковые крепления. Данный болт разрушается при пуске, так как на нем установлена специальная хрупкая гайка. При помощи анализа кинематики компания ATK быстро создала проектное решение, в котором крепления отводились нужным образом. «Основной целью было применить модуль NX Motion для создания временной последовательности пуска ракеты и обратного движения креплений. Нам удалось это сделать», – отмечает он.
Затем инженеры провели расчеты методом конечных элементов. В компании ATK имелся широкий выбор конечно-элементных препроцессоров и решателей. В рамках инициативы по углублению интеграции инженерных расчетов и конструирования компания ATK работает над унификацией применяемых CAE-систем. Решения NX CAE и NX Nastran® стали стандартными приложениями, которые используются совместно с другими приложениями при решении задач, не поддерживаемых системой NX. «Таким образом, каждый инженер работает в системах, выбранных в качестве стандарта предприятия, а не в той, которая ему больше нравится, – поясняет Кристенсен. – Это приводит к снижению затрат – нам не приходится заниматься поддержкой различных решений со сходной функциональностью, и это облегчает обмен результатами расчетов между исполнителями».
На основе конструкторской модели задней части твердотопливного ускорителя компания ATK создала конечно-элементную модель в системе NX CAE. «Многие системы конечно-элементного анализа плохо справляются с расчетом сборок, а в NX таких проблем нет», – отмечает Кришнан. По его мнению, главное преимущество решения NX CAE заключается в том, что вносимые в сборку изменения передаются в конечно-элементную модель. «Особенно хотелось бы отметить, что можно вносить изменения в модель и передавать их в среду конечно – элементного анализа, – говорит Кришнан. – Такая передача выполняется безошибочно. Конечно-элементная сетка при этом автоматически перестраивается, и это очень удобно. Кроме того, сохраняется ассоциативность.
Все наложенные в сборке связи сохраняются и в конечно-элементной модели. Поэтому вам не приходится проверять правильность расчетной кинематической модели».
Кроме того, компания ATK оценила удобство создания геометрии в системе NX CAE. «Нам понравилось то, что можно очень быстро моделировать болты в виде балочных и звездообразных элементов, – поясняет Кришнан. – Мы берем детали, которые фактически свободно плавают в пространстве, и накладываем на них связи при помощи инструмента, позволяющего выбрать все поверхности или ребра отверстия под болт. Затем балочные элементы создаются автоматически. Это экономит массу времени».
Компания ATK выполнила ряд КЭ-расчетов прочности пусковых креплений, но в основном метод КЭ применялся для расчета конической секции ускорителя, являющейся местом соединения ракеты со стартовым сооружением. Данная секция должна выдерживать вес всей ракеты (осевая нагрузка от пустой ракеты превышает 900 тонн, а от заправленной – почти 3200 тонн), а также ветровые нагрузки, в том числе и от ураганного ветра. Таким образом, расчетные нагрузки оказались огромными. «Мы еще никогда не сталкивались с такими колоссальными нагрузками на коническую секцию», – отмечает Кришнан.
Помимо экономии времени, еще более важным преимуществом реализованного в компании ATK интегрированного процесса проектирования и расчетов в системе стала полная уверенность в точности расчетной модели. «Мы были полностью уверены в том, что все выполняемые в NX построения точно передавались в модуль КЭ анализа и что мы рассчитывали именно актуальный вариант конструкции», – отмечает Кришнан. Благодаря этому компания ATK не теряла время на проверку моделей. «Кроме того, одна из проблем моделирования контактных взаимодействий в большой конечно-элементной сборке заключается в необходимости абсолютно точного совмещения деталей». При работе в NX детали в расчетной модели уже совмещены. Мы не тратим силы и время на создание сопряжений и размещение всех деталей. Они всегда находятся в правильном положении». Кроме того, данный процесс в целом уменьшает число возможных ошибок, так как не приходится передавать данные между различными системами.
Интеграция расчетов в процесс проектирования предполагает применение решения Teamcenter с целью управления задачами инженерного анализа. В хранилище данных Teamcenter записываются расчетные модели, отчеты и ссылки на структуру изделия. «Благодаря этому мы всегда рассчитываем нужные детали и варианты конструкций, а расчеты синхронизированы с вносимыми конструк-торскими изменениями, что сокращает необходимость в повторном анализе», – отмечает Кристенсен. Компания применяет Teamcenter для управления и процессами проектирования, и расчетными проектами. Решение Teamcenter для подготовки отчетов и аналитики отслеживает состояние проекта («по графику», «возможно отставание», «имеется отставание»), время выполнения и долю результатов, полученных с первого раза.
Кристенсен подводит итоги внедрения NX в качестве стандартного инструмента инженерного анализа и углубления интеграции между конструированием и расчетами: «Интеграция САЕ-решений на ранних этапах разработки изделия сокращает сроки проектирования, а также позволяет нам уделять основное внимание общей продолжительности конструкторской разработки, а не только продолжительности требуемых расчетов. Мы отмечаем существенное сокращение затрат и рост производительности благодаря тщательно продуманному стратегическому решению о стандартизации CAE-систем. Наконец, средства инженерного анализа наиболее эффективны, когда конструкторы применяют их на ранних этапах разработки».
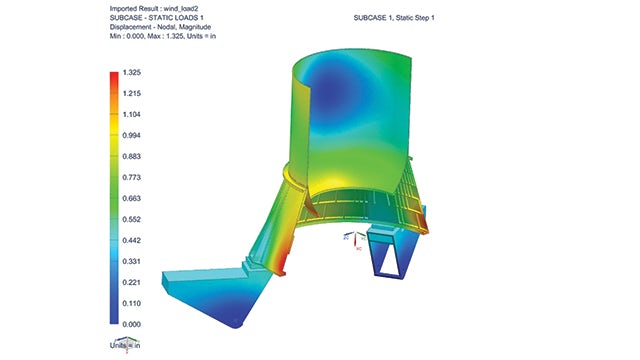
Bringing CAE into the PLM environment
ATK has used product lifecycle management (PLM) technology from Siemens Digital Industries Software for nearly a decade, utilizing NX™ software for design, Simcenter ™ software for performance simulation and Teamcenter® software to manage product information and processes. “We’ve had a long-standing partnership with Siemens Digital Industries Software,” says Ramesh Krishnan, a senior staff engineer in the ATK’s Engineering Processes and Tools group. “It started with visionary leadership who saw the benefits of an integrated system.”
In recent years, the group has been working to better integrate analysis into the design process. “Our challenge is to integrate CAE [computer-aided engineering] engineers early in the product development cycle so we can impact design,” says Nathan Christensen, senior manager of Engineering Tools and Analysis at ATK. “This can be a tall order given our nature as engineers and the complexity of our tool set.” The work being done for the SLS program related to the advanced booster rocket’s nozzle offers a good illustration of how they are meeting this challenge.
“The size of the nozzle is going to increase quite a bit to get better performance out of our motors,” explains Krishnan. “There are a lot of structures that a larger nozzle could possibly hit on its way up off the pad.” The aft end of the booster has a skirt, and attached to that skirt are launch mounts that hold the rocket in place while it is on the launch pad. ATK is designing retractable mounts – a first for ATK – that will retract at launch so the nozzle won’t hit them.
Using NX, ATK modeled the aft end of the booster, including the skirt and the retractable launch mount assembly. That digital geometry was then used for two different types of analysis, motion analysis and finite element analysis (FEA).
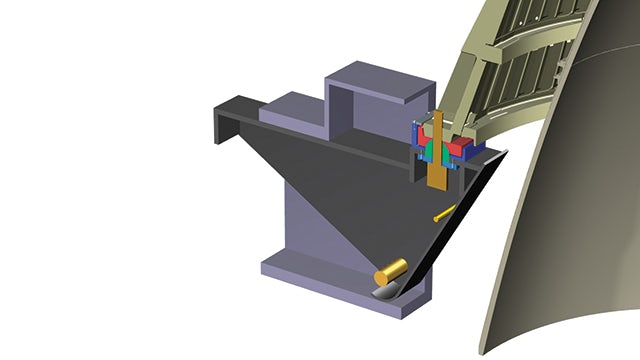
Retractable mounts and hurricane-force winds
ATK used Simcenter 3D Motion to simulate the movement of the launch mounts during the rocket’s lift off. “For the speed of the rocket, we used a curve that we input into Excel and then linked the motion simulation speed to that spreadsheet,” Krishnan explains. “That was thrust versus time, and it worked quite well. The rocket took off with appropriate acceleration.”
Next, the team undertook FEA. ATK had access to numerous FEA preprocessors and solvers. As part of the move to better integrate analysis and design, ATK is working to consolidate its CAE tools, making Simcenter 3D and Simcenter™ Nastran® software the standard applications and filling in with other solutions when necessary. “This way, engineers will use company standards, not favorites,” Christensen explains. “It should reduce the costs we have now of supporting multiple tools with similar functionality, and it will facilitate the hand-off of work between analysts.”
Starting with design geometry, ATK used Simcenter 3D to prepare the finite element model of the booster rocket’s aft assembly. “Many finite element modeling packages don’t handle assemblies very well, but Simcenter 3D does,” Krishnan explains. The best part of working with Simcenter 3D, in his opinion, is that changes made to the assembly model are maintained in the finite element model. “What’s really nice is the ability to make modifications in the modeling portion and transfer those over to FEA,” says Krishnan. “It’s very seamless. The mesh automatically updates and it’s very convenient. Also, you maintain associativity. All the connections you’ve made in the assembly stay in the assembly all the way through the FEA. You don’t have to try to move stuff around in the FEA.”
ATK also liked the ease of creating geometry using Simcenter 3D. “We like that we could model the bolts very quickly as beam elements and spider elements,” Krishnan explains. “We could take these parts that were free-floating in space and tie them all together with a tool that allows you to select all surfaces or edges of the bolt hole, and it automatically creates beam elements. That saved a lot of time.”
Although ATK did some FEA to determine whether the launch mounts were strong enough to handle their loads, more of the FEA was directed at the aft skirt, the interface between the rocket and the launch pad, which must withstand the weight of the rocket (2 million pounds axial load when empty of fuel; 7 million pounds when full) as well as wind loads (hurricane force). The loads involved were huge. “We’ve never dealt with loads of this magnitude in an aft skirt before,” says Krishnan.
In addition to saving time, the more important benefit to ATK of integrated NX design and Simcenter 3D analysis was that it gave the company confidence that its model was accurate. “We had confidence that what we drew using NX was coming right over to the finite element package and that’s what we were analyzing,” Krishnan explains. ATK spent less time checking analysis model thanks to that. “Also, one of the problems with modeling contact in large finite element assemblies is you have to make sure you’re line-online. With Simcenter 3D, you’re line-online from the beginning. There’s no fuss to maintain contact and make sure everything is in the correct location. It’s always in the correct location.” In addition, this process is less error-prone in general since there are no translations between software packages.
Integrating analysis into the design process includes the use of Teamcenter for managing CAE workflows, as well as the use of the Teamcenter data vault to store CAE models, results, reports and links to the product structures. “This helps ensure that we don’t analyze the wrong parts or configurations, and that analysts stay insync with design changes, reducing CAE rework,” notes Christensen. As with the company’s design process, Teamcenter is also used to keep analysis projects on-track. The Teamcenter solution for reporting and analytics is used to track project status (on-time, projected late, and late), cycle time and first-pass yields.
Christensen summarizes the effect of standardizing on Simcenter 3D for analysis, and of better integrating analysis and design this way: “Integrating CAE tools early in product development shortens the design cycle, and lets us focus on overall design cycle times instead of analysis cycle times. Also, we believe that significant cost savings and productivity gains can be accomplished with careful and strategic CAE tool standardization. Most important, CAE is most effective if engaged early with the design team.”
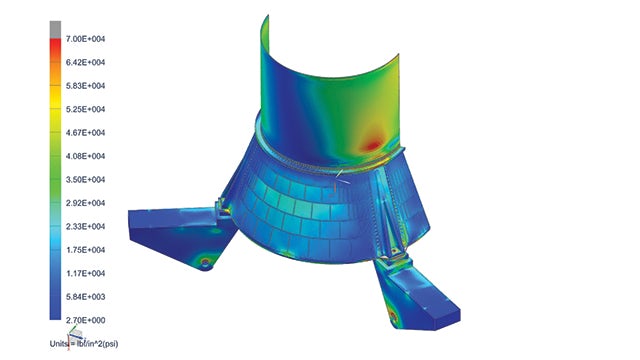
Мы отмечаем существенное сокращение затрат и рост производительности благодаря тщательно продуманному стратегическому решению о стандартизации CAE-систем.
Группа компаний ATK Aerospace