Компания применяет систему Simcenter для проектирования безопасных и эффективных самолетных шасси
Siemens PLM Software помогла компании GKN Aerospace Fokker Landing Gear сократить сроки проектирования на 30%
GKN Aerospace Fokker Landing Gear
Компания GKN Aerospace — один из ведущих мировых поставщиков первого порядка, выпускающих авиационные комплектующие. Заказчиками компании являются ведущие мировые авиа-производители. GKN Aerospace разрабатывает изготавливает и поставляет широкую линейку современных авиакосмических систем, комплектующих и технологий, применяемых в вертолетах, самолетах бизнес-авиации, самых популярных узкофюзеляжных авиалайнерах и крупнейших пассажирских самолетах. Легкие композитные материалы, аддитивное производство, инновационные конструкции двигателей и умное остекление помогают снизить объем вредных выбросов и массу самолета, а также повышают комфорт пассажиров. GKN Aerospace — лидер рынка авиационных конструкций, систем авиадвигателей, остекления и электропроводки.
http://www.gknaerospace.com- Штаб-квартира:
- Helmond, Netherlands
- Решения:
- Simcenter Products, Simcenter Amesim
- Отрасль:
- Aerospace & defense
Коммерческий успех всецело зависит от сроков и себестоимости процесса разработки.
GKN Aerospace Fokker Landing Gear
Высокая безопасность и отличные технические характеристики при минимальной массе
Полеты на огромных стальных птицах — одно из величайших достижений человечества. Говоря о самолетах, большинство людей представляют себе крылья, двигатели, фюзеляж или хвост. Однако, как птица не способна выжить без сильных ног, на которые она приземляется, так и самолету совершенно необходимо прочное и надежное шасси.
Конструкции шасси отличаются большим разнообразием. Поскольку выбор конкретной конструкции оказывает большое влияние на все характеристики самолета в целом, шасси необходимо проектировать совместно со всеми остальными узлами летательного аппарата.
Очевидно, что основное предназначение шасси — снижение ударных нагрузок путем поглощения и рассеяния кинетической энергии. Кроме того, в шасси предусмотрены подвеска, тормоза и возможность руления — все это необходимо для передвижения самолета по земле. В большинстве случаев шасси делают убирающимся (особенно на скоростных самолетах) для снижения сопротивления воздуха в полете. Однако убирающиеся шасси оказываются довольно тяжелыми: на них приходится до 3% общей массы самолета. Шасси должно вписаться в ограниченный объем, что особенно актуально для военной авиации, и надежно интегрироваться с самолетными системами.
Снижение массы и габаритов без ухудшения технических характеристик и при сохранении высокого уровня безопасности — очень непростая задача. Наконец, проектирование шасси не должно задерживать весь процесс создания самолета. Поэтому предприятиям необходимы решения, позволяющие максимально быстро проанализировать как можно больше различных вариантов конструкции.
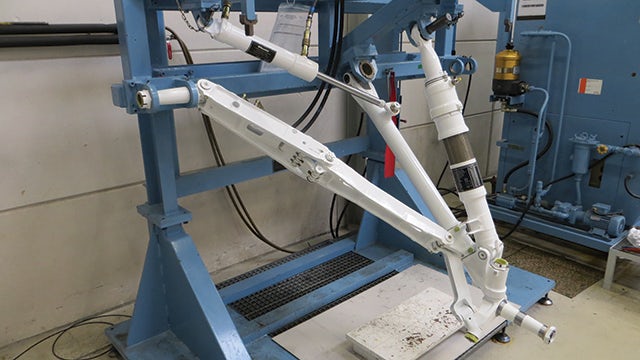
Более 30 лет опыта
Инженеры компании GKN Aerospace Fokker Landing Gear (Хельмонд, Нидерланды) отлично освоили искусство создания безопасных и эффективных самолетных шасси, которые они поставляют производителям авиационной техники. Уже более 30 лет специалисты накапливают опыт конструкторско-технологической подготовки, изготовления, текущего и капитального ремонта шасси самолетов и вертолетов. Компания GKN Landing Gear успешно решает задачи своих заказчиков благодаря умению разрабатывать уникальные конструкции, оптимизированным процессам проектирования, соблюдению самых жестких квалификационных и сертификационных требований и стандартов, применению самых современных производственных технологий и наличию прекрасной ремонтной базы. В настоящее время компания поставляет комплектующие для таких известных летательных аппаратов, как ударный истребитель Lockheed Martin F-35 Lightning II и боевой вертолет Boeing Apache AH-64. Компания GKN Landing Gear инвестирует серьезные средства в исследования и разработки, ставя перед собой цель в ближайшем будущем начать поставки несущих деталей шасси из композитных материалов.
Специалист отдела инженерной динамики доктор Берт Вербеек (Dr. Bert Verbeek) и коммерческий директор компании GKN Landing Gear Гуус Колстер (Guus Kolster) накопили многолетний опыт работы. Они неоднократно сталкивались с тем, что именно опыт является решающим фактором при выборе поставщика комплектующих. Они отмечают, что за последнее десятилетие значительно возросли требования к сокращению сроков и себестоимости разработок. Все эти тенденции оказывают существенное влияние на процессы проектирования. «В отличие от потребительских товаров объем выпуска шасси невелик, — рассказывает Колстер. - Коммерческий успех всецело зависит от сроков и себестоимости процесса разработки. Поэтому метод проб и ошибок недопустим.
Очень важно создать четкий процесс, основанный на точном численном моделировании на ранних этапах разработки. Благодаря этому мы оптимизируем конструкцию еще до изготовления первого опытного образца».
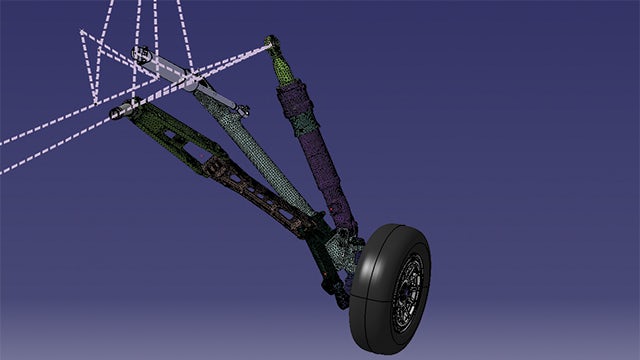
Укрепление репутации и экономия времени на 30%
Основной целью деятельности компании Siemens PLM Software является создание мощных программных средств численного моделирования. На протяжении многих лет решения из пакета Simcenter™ применяются в рамках стандартного процесса разработки в компании GKN Landing Gear. Среди них — система LMS Virtual.Lab™ Motion, выполняющая 3D-расчеты динамики множества тел, и система 1D-мультифизических расчетов LMS Imagine.Lab Amesim™.
Вербеек является одним из инженеров, начинавших успешную совместную работу между компаниями GKN Landing Gear и Siemens. «До этого мы использовали другую программу для 3D-расчетов динамики множества тел. Приходилось разрабатывать много дополнительных программ, реализующих модели процессов демпфирования и модели других систем, — рассказывает он. - Процесс был длительным, трудоемким и приводил к ошибкам. Кроме того, передача опыта новым сотрудникам была крайне затруднена. Теперь же при помощи LMS Amesim эта задача решается несравненно легче. Мы поняли, что нам требуются более профессиональные и оптимизированные процессы. Это не только упрощает жизнь, но и расширяет возможности совместной работы с партнерами по отрасли».
Системы LMS Virtual.Lab Motion и LMS Amesim широко востребованы в авиационной промышленности, что стало одним из важнейших аргументов в пользу выбора именно этих решений. «Поскольку разработка шасси выполняется параллельно с проектированием остального самолета, нам нужны способы эффективного обмена информацией и идеями с нашими партнерами, — отмечает Вербеек. - Наши заказчики предоставляют нам информацию, необходимую для расчетов нагрузки от шасси на опорную поверхность и на планер, а мы даем им модели, позволяющие выполнять численное моделирование всего самолета целиком. Делать это гораздо легче, если использовать аналогичные платформы или хотя бы решения, способные обмениваться данными друг с другом. Когда в ходе выполнения проекта мы проводим совещание с заказчиком для обмена идеями и обсуждения предварительных результатов, наша репутация упрочняется, когда мы демонстрируем использование профессионального и известного решения, а также представляем данные в привычном заказчику формате».
Внедрение нового решения никогда не бывает простым делом. Требуется обучение и привыкание пользователей к новому графическому интерфейсу, нужно создать комплект моделей и разработать библиотеки испытанных и проверенных деталей и узлов. «Поддержка профессионалов из Siemens PLM Software помогла нам успешно освоить новую систему, — говорит Вербеек. - Кроме того, наши специалисты выполняют небольшие проекты по повышению точности моделирования отдельных деталей».
Существенного сокращения сроков разработки удалось добиться не только благодаря внедрению новых программ, но и эффективному сотрудничеству с инженерами Siemens PLM Software. «Когда мы сравнили процесс с использованием LMS Virtual.Lab Motion и LMS Amesim с тем, что у нас было раньше, то выяснили, что экономия времени составила не менее 30%. Мы используем сэкономленное время для углубленного анализа, уточнения физических характеристик наших моделей и проведения дополнительных видов численного моделирования. Мы работаем над созданием параметрических 3D-моделей основных вариантов конструкции шасси, а также параметрических 1D-библиотек амортизаторов и шин».
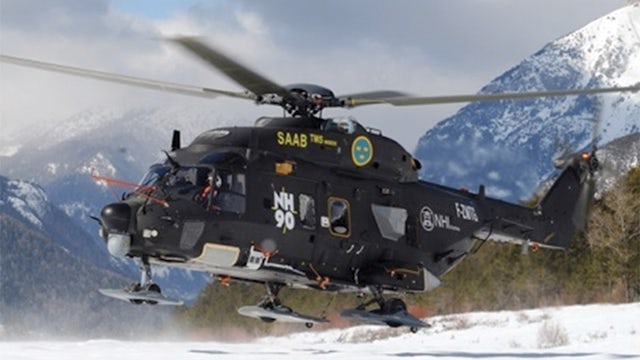
Автоматизация процесса оптимизации
В настоящее время весь процесс численного моделирования полностью выстроен и отлично работает. Реализован обмен данными с другими системами, построены параметрические модели и созданы циклы оптимизации по критериям технических характеристик, массы и себестоимости. Теперь ставится задача перехода на новый уровень — к автоматизации процесса. Это также выполняется в тесном сотрудничестве со специалистами Siemens PLM Software. «Во-первых, мы все еще работаем над расширением и улучшением наших библиотек, — отмечает Вербеек. - Мы также создаем дополнительные 1D-модели амортизаторов, многотельные 3D-модели и CAD-модели отдельных деталей. И мы рассматриваем новые варианты моделирования явления шимми шасси. Во-вторых, мы создали скрипты, выполняющие весь процесс численного моделирования без вмешательства пользователя. И эту работу мы тоже начинали при поддержке специалистов Siemens PLM Software».
Инженеры твердо убеждены, что их усилия приведут к существенному росту производительности. «Перейдя на профессиональное программное обеспечение, мы уже сократили сроки разработки примерно на 30%, а автоматизация сократит их еще больше, — считает Вербеек. - Пока мы рассчитываем только один заранее выбранный вариант конструкции — на разработку большего числа вариантов не хватает времени. Поэтому мы по-прежнему в значительной степени полагаемся на интуицию и опыт. Мы уверены, что эта ситуация изменится после внедрения скриптов автоматизации».
Колстер также настроен очень оптимистично: «Если сейчас мы можем рассматривать три-четыре принципиально разных конструкции шасси в 3D, включающие в себя модели нескольких видов амортизаторов, то, по моим оценкам, после автоматизации мы за то же время сможем анализировать от 15 до 20 вариантов».
Мы поняли, что нам требуются более профессиональные и оптимизированные про- цессы. Это не только упрощает жизнь, но и рас- ширяет возможности совместной работы с партнерами по отрасли.
GKN Aerospace Fokker Landing Gear