Сплоченная работа и единая среда проектирования позволили получить колоссальные результаты при производстве мотоциклов
Despite the increasing complexity of its products, Ducati reduced its development cycle by one year through the use of NX and Teamcenter
Ducati
Ducati Motor Holding S.p.A — ведущий разработчик и производитель мотоциклов высокого класса.
http://www.ducati.com- Штаб-квартира:
- Bologna, Borgo Panigale, Italy
- Решения:
- NX, Teamcenter
- Отрасль:
- Automotive & transportation
Мы не можем представить себе работу без Teamcenter.
Ducati
Пример внедрения: Ducati
Престижная марка со страстными поклонниками
Ducati Motor Holding S. p.A. (Ducati) – была основана в 1926 г. и занималась производством деталей для развивавшейся радиопромышленности. После второй мировой войны компания начала выпуск двигателей и небольших мотоциклов, постепенно превратившись в одну из самых значительных и популярных марок дорожных и гоночных мотоциклов. Сегодня Ducati выпускает около 40 тыс. мотоциклов в год. Ее линейка продукции состоит из шести классов, включающих 17 моделей среднего и верхнего ценового сегмента.
Из 1000 сотрудников Ducati около 200 занимаются исследованиями и разработками, на которые компания ежегодно выделяет значительные средства. Инженерный персонал состоит из примерно 90 человек, 60 из них занимаются конструированием. Кроме того, Ducati работает по всему миру и имеет широкую сеть партнеров и поставщиков, на которых приходится 92% производства. Любая ошибка или задержка при передаче информации может привести к росту сроков и затрат, поэтому Ducati интенсивно стремилась к более тесной интеграции между всеми разработчиками изделий.
Среди технологий, внедренных в компании для достижения данной цели, применяются два решения от Siemens PLM Software: системы NX™ и Teamcenter®. NX – применяемая в компании система автоматизированного проектирования (CAD) – используется для создания цифровых моделей и управления всей трехмерной сборкой мотоцикла. Teamcenter служит решением по управлению жизненным циклом изделия (PLM), обеспечивая надежный обмен данными как внутри компании, так и с ее поставщиками.
Пресс-формы, кузов и электропроводка – все в NX
«NX – это инструмент, который мы применяем с момента появления замысла нового проекта и до его завершения, – рассказывает Пьеро Гиусти (Piero Giusti), директор по информационным технологиям отдела разработок Ducati Motor Holding. – NX используется для проектирования многих узлов мотоциклов, в том числе колес, шасси и кузова, а также оригинальных деталей – фактически всего, за исключением двигателя».
В настоящее время в компании Ducati имеется свыше 50 рабочих мест NX. «Основные преимущества NX – гибкость и простота в использовании, – отмечает Гиусти. – Под гибкостью я понимаю то, что система позволяет создавать 3D-модели различными способами, не ограничивая вас каким-то одним подходом. В NX с синхронной технологией реализован гибридный способ моделирования, при котором не приходится выполнять полную параметризацию, поэтому пользователь имеет полную свободу в выборе путей достижения конечного результата».
Инженеры Ducati широко используют функционал NX по 3D-проектированию электропроводки. Система позволяет им проверять прокладку проводов внутри виртуальной сборки, что снижает до минимума возможные ошибки на последующих этапах. «Следующим шагом станет интеграция электросхемы, что позволить отказаться от отдельной программы, наличие которой неизбежно приводит к проблемам с обновлением данных и ссылками, – добавляет Гиусти. – Теперь мы можем разрабатывать электросхемы при помощи соответствующего функционала NX. Затем схема передается в приложение NX для проектирования проводки, объединяя все данные по электрике с остальной кон-струкцией. Наконец, при помощи решения NX для проектирования разводки кабелей мы подготавливаем документацию по монтажу проводки. В NX реализуется единый подход ко всему этому процессу».
Защищенный обмен данными с Teamcenter
NX поддерживает совместную работу как разработчиков внутри компании, так и взаимодействие со сторонними поставщиками, среди которых – производители пресс-форм и таких важнейших узлов, как колесная вилка. Благодаря использованию Teamcenter компания Ducati собирается достичь еще более тесной интеграции процессов совместной работы. «Нам все чаще приходиться обмениваться данными и моделями с поставщиками, – поясняет Гиусти. – Для ряда наших давних партнеров мы рассматриваем возможность предоставления им прямого доступа к хранящейся в нашей системе информации, чтобы мы могли еще больше сократить сроки разработки за счет параллельной работы поставщиков и наших конструкторов. Через несколько лет мы объединим в единую систему всех наших стратегических поставщиков, предоставляющих нам свои технологии». Компания Ducati уже начала данный процесс с рядом своих поставщиков.
Внутри самой компании Teamcenter уже широко применяется. Teamcenter используется на 250 рабочих местах для доступа к информации, создаваемой отделом проектирования. Кроме того, компания внедрила Teamcenter на складе Saima в г. Модена. Все мотоциклы поступают на данный склад для выполнения ряда сборочных операций, проверки наличия запчастей или исправления в случае неверной сборки./p>
Персонал склада имеет доступ к хранимой в Teamcenter информации по выделенной линии. Они могут просматривать чертежи, графики и сборочные таблицы по всем завершенным изделиям. Пользователи системы на данном складе выполняют небольшие сборочные операции. Как правило, это установка деталей кузова и уникальных элементов оформления, но время от времени им приходится вносить в конструкцию и более существенные изменения. Поэтому необходим доступ к документации на изделие. «Следует отметить, что персоналу Saima было очень легко освоить Teamcenter, – отмечает Гиусти. – То, что они не проходили специального обучения, свидетельствует об интуитивной понятности и простоте работы с Teamcenter».
«Мы не можем представить себе работу без Teamcenter. По сравнению с ранее использовавшимся процессом, требовавшим огромного количества бумаг, мы полностью отказались от бумажных документов и избавились от шкафов для их хранения. При помощи Teamcenter мы реализовали компьютерную систему управления данными, предоставляющую контролируемый доступ к информации с разделением по ролям пользователей, а также высокий уровень безопасности данных».
Более быстрое создание более сложных мотоциклов
Применяемое в компании Ducati PLM-решение значительно ускорило темпы разработки изделий, что позволило спроектировать новую модель заметно быстрее, несмотря на существенный прирост объема используемой в ее конструкции электроники и соответствующего программного обеспечения. Сегодня на мотоциклах может устанавливаться до шести или даже семи электронных блоков управления (ЭБУ), регулирующих работу подвески, трансмиссии, тормозной системы, а также контролирующих устойчивость на дороге. «Все эти системы взаимодействуют друг с другом и ими нужно надежно и эффективно управлять, – отмечает Гиусти. – Теперь наши требования к управлению конфигурациями изделия аналогичны применяемым в автомобилестроении или авиационно-космической отрасли».
Несмотря на огромную сложность изделий, компания Ducati на целый год сократила срок разработки новых моделей мотоциклов. «Наш цикл разработки в среднем сократился с 36 …40 до всего лишь 24 месяцев в основном благодаря инструментам, предоставленным Siemens PLM Software, – говорит Гиусти. – Кроме того, теперь мы можем ежегодно обновлять все выпускаемые модели. Таких результатов было бы невозможно достичь, применяя традиционные методы конструирования».
Комплекс PLM-решений от Siemens PLM Software позволил компании Ducati объединить все подразделения и процессы: изготовление опытных образцов, производство, работу складов, поставки запчастей и принадлежностей. «Благодаря интеграции и параллельному выполнению всех этих процессов теперь мы разрабатываем аксессуары одновременно с проектированием самого мотоцикла, – рассказывает Гиусти. – Ранее на подготовку выпуска аксуссуаров на рынок уходило от 6 до 12 месяцев. Теперь же они оказываются готовыми одновременно с мотоциклом, что дает заметный синергетический эффект при продажах».
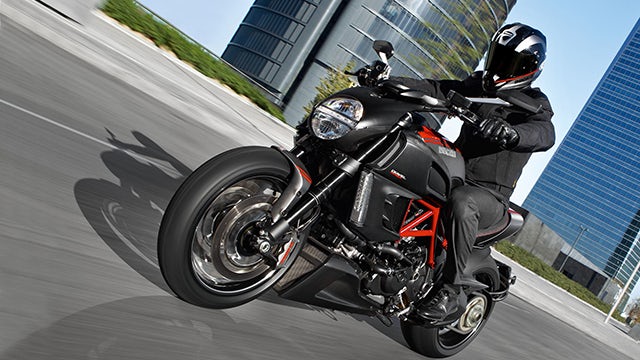
Molds, body and cabling – all with NX
“NX is the tool we use from the moment we start thinking about a new project up to its completion,” explains Piero Giusti, information technology manager for R&D at Ducati Motor Holding. “NX is used to design many different motorbike components, including the wheels, the chassis and the body, as well as custom parts – virtually everything except the engine.”
There are currently more than 50 NX workstations at Ducati. “The key benefits of NX are flexibility and ease of use,” Giusti says. “By ‘flexibility,’ I mean that it lets you generate 3D models with different methods, without constraining you to a fixed approach. NX with synchronous technology is a hybrid approach that avoids having to parameterize everything, so the user is free to choose how to achieve the final result.”
Ducati engineers use the NX 3D wiring functionality extensively. It allows them to verify cable routing inside the virtual assembly, minimizing possible routing issues downstream. “The next step will be the integration of the wiring diagram to eliminate the use of separate software, which inevitably causes problems with updating and referencing,” Giusti adds. “We have schematized the flow so that we can create wiring diagrams using the NX schematic functionality. After that, the diagram is passed on to the NX wiring application to incorporate all electrical information into the design. And finally, using the NX electrical routing solution, we prepare the documentation for cabling installation. NX lets us cover the entire process with an integrated approach.”
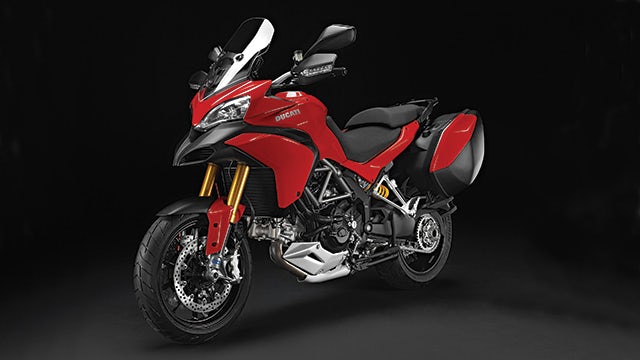
Secure data sharing with Teamcenter
NX supports closer collaboration both within the internal development team as well as with external suppliers, who include companies that manufacture molds and key components such as the fork. Ducati expects to achieve even closer collaboration through the use of Teamcenter. “We increasingly need to exchange model data with these suppliers,” explains Giusti. “With some of our long-term partners, we are investigating the possibility of providing them with direct access to the information in our system so that we can further reduce development time by having them work in parallel with our designers. Within a few years, we will integrate all of our strategic suppliers that produce technology on our behalf.” Ducati has already begun this process with several of its suppliers.
Within Ducati, the use of Teamcenter is already widespread. The company has 250 workplaces that use Teamcenter to access information generated by the engineering department. The company has also deployed Teamcenter at its Saima warehouse in Modena. All motorbikes go through this site for some assembly operations, spare parts verification, or modifications due to mounting errors.
The warehouse staff has access to the information stored in Teamcenter through a dedicated line. They can view drawings, diagrams and assembly tables for all finished products. The users at this site execute minor assembly operations, typically installing body parts and custom elements, but occasionally they perform more significant modifications as well. The users need access to product documentation. “It is worth noting that it was easy for the Saima staff to learn to use Teamcenter,” says Giusti. “The fact that they had no specific training bears witness to the intuitiveness and ease of use of Teamcenter.”
“We couldn’t imagine working without Teamcenter. From our previous process that required tons of paper, we have eliminated paper and filing cabinets. Using Teamcenter we have implemented a digital information management system with traceable, role-based access, and a high degree of intrinsic security.”
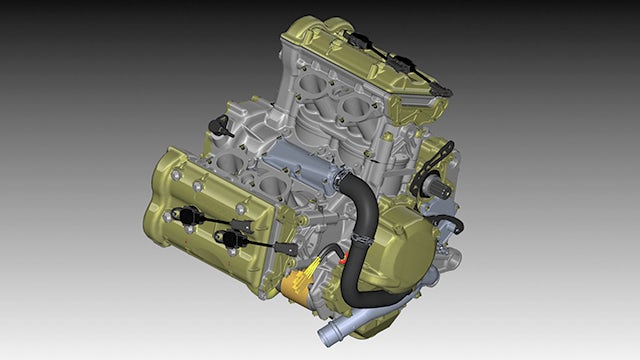
More complex motorbikes, developed faster
Ducati’s PLM solution has greatly accelerated the pace of product development, enabling the company to develop a new model much faster even though the use of electronics and related software has grown substantially. Today’s motorbikes can have up to six or seven electronic control units (ECUs) for suspension, transmission, braking and stability. “All these systems are interacting and must be managed in an efficient and reliable way,” says Giusti. We now have product configuration handling requirements very similar to those of automotive or aerospace companies.”
In spite of greater product complexity, Ducati has cut one year off the development cycle for new motorbikes. “Our design and development cycle has been reduced from an average 36 to 40 months to just 24 months, mainly thanks to the tools provided by Siemens Digital Industries Software,” says Giusti. “We are also able to update all existing models at annual intervals. It would be unthinkable to achieve such results using conventional design methods.”
Siemens Digital Industries Software’s PLM suite has enabled Ducati to integrate all departments and operations: prototypes, production, warehouse, spare parts, and accessories. “By integrating and parallelizing all these processes, we can now develop accessories concurrently with the motorbike,” says Giusti. “In the past, it used to take 6 to 12 months before accessories were marketed. Now they are ready together with the bike, generating significant sales synergies.”
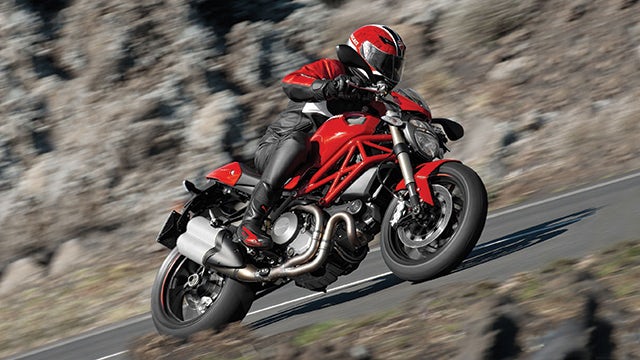
Основные преимущества NX — гибкость и простота в использовании.
Ducati