Yanghe Distillery migliora l'efficienza e la qualità della produzione e riduce i costi con le tecnologie APS, MES e LIMS di Siemens
Le soluzioni Opcenter supportano i principali produttori globali di distillati nel processo di trasformazione digitale
Yanghe Distillery
Yanghe Distillery è stata inserita per tre anni consecutivi nella classifica delle 500 maggiori aziende cinesi di Fortune China ed è stata menzionata nel Financial Times Global 500 nel 2012. Nel 2014 e nel 2015 è entrata nel ranking "BrandZ™ Top 100 Most Valuable Chinese Brands" e nel 2017 si è posizionata al terzo posto nella Brand Finance Spirits 50.
http://www.yangheglobal.com/- Sede centrale:
- Suqian, Jiangsu, China
- Prodotti:
- Opcenter, Laboratory
- Settore industriale:
- Beni di consumo e vendita al dettaglio
Leader mondiale nel settore dei distillati
Jiangsu Yanghe Distillery Co., Ltd. (Yanghe) si trova a Suqian, capitale cinese dei distillati, e vanta un patrimonio totale di 7 miliardi. L'azienda conta quasi 30.000 dipendenti e dispone della più grande rete di vendita nel settore dei distillati in Cina. Questa rete è costituita da più di 9.000 addetti alla vendita diretta, quasi 10.000 distributori e 360.000 unità incaricate degli acquisti di gruppo o all'ingrosso. La società conta 2 milioni di punti vendita partner e dispone di punti vendita diretti in 33 province, città e regioni autonome, 333 città-prefetture e 2.851 contee e distretti in tutto il paese.
È l'unica azienda del settore dei distillati in Cina a essere rinomata per due "famosi liquori cinesi" e due "marchi cinesi storici" a Yanghe e Shuanggou. Il vino Shuanggou, le cui origini risalgono a 18 milioni di anni fa, nella zona di Shuanggou Xia Caowan, è la quintessenza del vino cinese. Le tre basi produttive, Yanghe, Shuanggou e Siyang, si estendono su una superficie totale di oltre 10 chilometri quadrati e contano più di 1.000 team di enologi, oltre 70.000 rinomate cantine vinicole e una capacità produttiva annua di 160.000 tonnellate di vino.
Con una capacità di stoccaggio pari a 1 milione di tonnellate di vino, Yanghe è il principale produttore di Baijiu in Cina e nel mondo. In termini di ricerca e sviluppo tecnologico, nel 2003 l'azienda ha applicato con successo la tecnologia dell'equilibrio molecolare per conferire morbidezza e rotondità ed è stata la prima azienda del settore a produrre un liquore extra-morbido, cosa che le è valsa una certa notorietà.
Nel 2017, Yanghe si è posizionata al secondo posto in Cina e al terzo posto a livello mondiale nella classifica "Top 50 Global Spirits Brand Value", facendo conoscere al mondo otto vini cinesi di lunga tradizione. Nel 2019 è entrata nel ranking "BrandZ™ Top 100 Most Valuable Chinese Brands", classificandosi al 48° posto per tre anni consecutivi, ed è stata inserita per la seconda volta tra i 500 maggiori brand a livello mondiale, scalando 175 posizioni rispetto all'anno precedente e classificandosi al 215° posto. Tra i 65 brand cinesi presenti nella lista, Yanghe si è classificata al 35° posto; in occasione della conferenza 2018 China Brand Value Evaluation, le azioni di Yanghe si sono posizionate al primo posto nella classifica dei valori del marchio dei prodotti cinesi, con un valore del marchio di 63,055 miliardi di yuan. Nel 2020, il valore del marchio si è posizionato al terzo posto nella classifica "2020 China Brand Value" per l'industria leggera e al secondo posto nella classifica relativa al settore dei distillati ed è entrato nella "Top 100 Brand Value of Chinese Listed Companies in 2020", dove si è classificato al 42° posto.
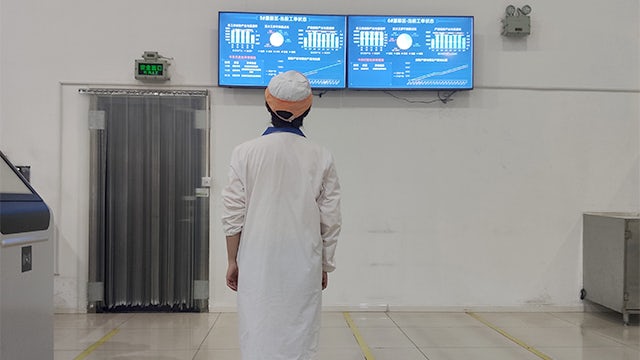
Progetto di digitalizzazione globale
I precedenti sforzi di digitalizzazione di Yanghe riguardavano principalmente i sistemi di gestione aziendale, tra cui la piattaforma di vendita, il sistema di pianificazione delle risorse aziendali (ERP), il sistema di gestione del magazzino (WMS) e il sistema di gestione dei trasporti (TMS). Nel 2018, Yanghe ha dato il via a un progetto globale di trasformazione digitale della produzione, noto come 5211 Smart Factory Project. Il progetto includeva sei aree di interesse principali: pianificazione, produzione, qualità, laboratorio, attrezzature e contabilità dei costi.
Tra gli obiettivi dell'azienda rientravano la standardizzazione della produzione e delle operazioni, la visualizzazione dei processi produttivi, la pianificazione intelligente della produzione, il controllo automatizzato dei processi, il perfezionamento delle procedure di contabilità dei costi di produzione e la tracciabilità della qualità.
Secondo le previsioni di Yanghe, il progetto dovrebbe semplificare il coordinamento lungo la catena di approvvigionamento, dai distributori ai fornitori di primo livello, attraverso un flusso di informazioni ininterrotto a tutti i livelli, dal piano di produzione alla consegna del prodotto. Il progetto mira a ottimizzare l'intero processo di monitoraggio e gestione della qualità attraverso l'approvvigionamento di materiali di qualità, l'efficienza produttiva e la riduzione dei costi di produzione e dei guasti alle apparecchiature.
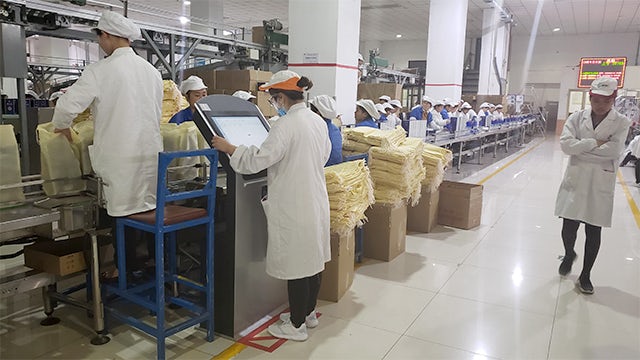
Problematiche aziendali e tecniche
Yanghe offre diversi prodotti e presenta processi aziendali complessi. In fase di studio del progetto di digitalizzazione, l'azienda ha identificato più di 100 problemi relativi a pianificazione, produzione, qualità, attrezzature e finanze e più di 40 opportunità per migliorare l'efficienza e ridurre i costi.
Un esempio è dato da un centro di condizionamento in loco conforme agli standard e alle procedure di ispezione a tutti i livelli, tra cui il controllo di qualità in-process (IPQC), il controllo di qualità del prodotto finale (FQC), il controllo di qualità in uscita (OQC) e il campionamento in laboratorio. Una delle sfide principali era legata al fatto che i dati delle ispezioni venivano registrati e condivisi in forma cartacea, il che non consentiva un'adeguata rapidità di azione in risposta ai risultati delle ispezioni e una gestione efficace.
Un altro esempio è rappresentato dal tipico processo di produzione dei distillati basato su una logica di flusso. A ciascuna linea di confezionamento corrisponde uno specifico processo di lavorazione, e ciascuna linea dispone di un sistema di codifica per garantire la tracciabilità del prodotto e di servizi outbound e inbound. Siccome Yanghe utilizzava registri manuali, la gestione dello stabilimento mancava di trasparenza.
Yanghe ha dovuto inoltre affrontare una sfida di natura tecnica: le apparecchiature di produzione erano molto vecchie e molte macchine non erano in grado di raccogliere direttamente i dati e non supportavano i controlli automatizzati. Gran parte delle apparecchiature stava attraversando una fase di transizione all'automazione. Per garantire la cooperazione tra le apparecchiature, sono stati applicati più sistemi con diverse interfacce.
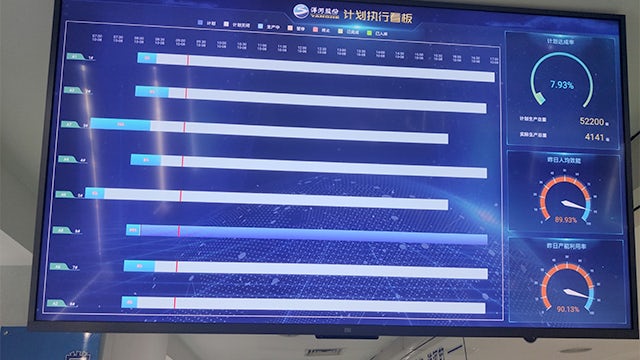
Scelta delle soluzioni Opcenter
In seguito all'approvazione del piano per la realizzazione della fabbrica digitale, l'azienda ha valutato diversi fornitori di soluzioni in Cina e all'estero. Le soluzioni Siemens Opcenter™ si sono rivelate quelle più adatte alla struttura complessiva del sistema, e l'accordo di collaborazione finale è stato confermato previo coordinamento tra Yanghe, Shanghai Huicheng, partner commerciale di Siemens, e Siemens stessa.
Sono diverse le ragioni che hanno portato alla scelta delle soluzioni Siemens. In primo luogo, Siemens offriva un sistema di esecuzione della produzione (MES), Opcenter Execution Process, realizzato su misura per le industrie di processo. Inoltre, Siemens offriva Opcenter Scheduling, che rispondeva ai requisiti di Yanghe in materia di pianificazione intelligente della produzione. Il portafoglio di soluzioni Siemens includeva inoltre un sistema di gestione delle informazioni di laboratorio (LIMS), Opcenter Laboratory, che Yanghe avrebbe potuto utilizzare per integrare i fornitori e ottimizzare la raccolta, l'analisi e il reporting dei dati di qualità in laboratorio e sulla linea di produzione. L'integrazione di MES, APS e LIMS all'interno di una piattaforma collaborativa avrebbe contribuito a migliorare l'accuratezza delle registrazioni contabili, avrebbe permesso di conoscere lo stato della produzione per ciascuna business unit e avrebbe ottimizzato l'efficienza operativa e produttiva, migliorando al contempo la qualità del prodotto.
Con un'ampia base di clienti nei settori del Food & Beverage e delle industrie di processo e un portfolio di soluzioni settoriali specifiche, Siemens dimostra di comprendere a fondo le esigenze degli utenti e offre soluzioni affidabili orientate al business e supporto tecnico a livello globale.
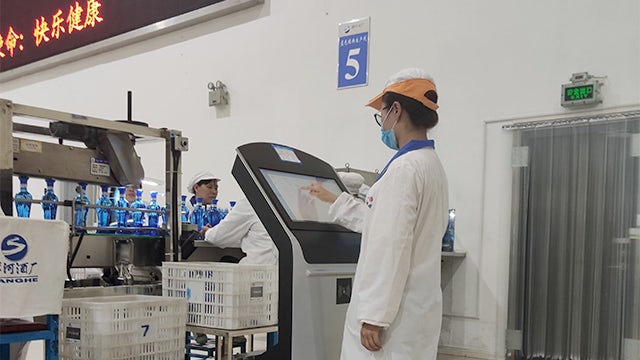
Implementazione del progetto di fabbrica intelligente
Siemens ha aiutato il team di progetto a valutare i requisiti aziendali di Yanghe e ha fornito assistenza a livello di pianificazione e progettazione dettagliata della soluzione globale. Sulla base delle funzionalità del software Opcenter e dei requisiti aziendali, il team di implementazione del progetto ha definito 13 modelli relativi a cinque aspetti, tra cui riparazione automatica, previsione in tempo reale, processo decisionale autonomo, analisi di modellazione e analisi di correlazione, per migliorare in modo sostanziale il controllo intelligente della produzione.
Per implementare il progetto della fabbrica intelligente, Yanghe ha sostituito un processo di pianificazione basato sui fogli di calcolo con il software Opcenter APS. Integrando le funzionalità del software con i processi aziendali esistenti, il team di progetto ha definito le regole per la pianificazione dei materiali e delle attrezzature richiesti, riducendo al minimo i tempi di configurazione complessivi per la produzione. Yanghe ha inoltre definito gli indicatori chiave di performance (KPI) e i relativi requisiti di reporting.
L'implementazione di Opcenter Execution Process ha offerto evidenti miglioramenti attraverso il controllo software automatizzato, che ha sostituito le operazioni manuali, e i dispositivi integrati, che raccolgono dati sulle quantità prodotte e le velocità operative di ciascun processo mediante strumenti e apparecchiature automatizzati.
Per i processi di controllo della qualità, Yanghe ha implementato le funzionalità Opcenter Laboratory per il controllo di qualità in entrata (IQC), la gestione dei codici a barre, la scansione automatica e il controllo di qualità in uscita (OQC) per costruire un sistema di raccolta delle informazioni sulla qualità e una piattaforma di gestione della qualità, in modo da garantire la tracciabilità della qualità a livello dell'intero processo, dai prodotti finiti e semilavorati alle materie prime.
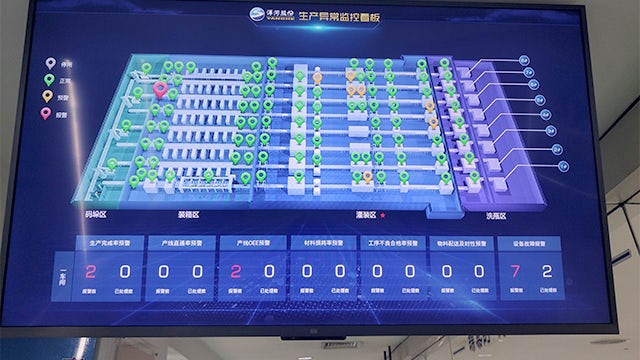