Yanghe Distillery mejora la eficacia y la calidad de la producción y reduce costes con la tecnología APS, MES y LIMS de Siemens
Las soluciones de Opcenter ayudan al fabricante líder mundial de bebidas alcohólicas destiladas en su transformación digital
Yanghe Distillery
Yanghe Distillery ha sido incluida en la lista de las 500 principales empresas chinas publicada por Fortune China durante tres años consecutivos y fue nombrada en la lista Financial Times Global 500 en 2012. La empresa fue elegida entre las «100 marcas chinas más valiosas» de BrandZ™ en 2014 y 2015 y ocupó el tercer puesto en el Brand Finance Spirits 50 en 2017.
http://www.yangheglobal.com/- Sede:
- Suqian, Jiangsu, China
- Productos:
- Opcenter, Laboratory
- Sector industrial:
- Productos de consumo y comercio minorista
Líder mundial de bebidas alcohólicas destiladas
Jiangsu Yanghe Distillery Co., Ltd. (Yanghe) se encuentra en Suqian, la capital del licor chino, con unos activos totales de 7000 millones. Yanghe cuenta con casi 30 000 empleados y ha creado la red de ventas más sólida de la industria de licores de China. La red tiene más de 9000 ventas directas, unos 10 000 distribuidores y 360 000 unidades de compra grupales o a granel. Dispone de dos millones de partners en punto de venta y los puntos de venta directos abarcan 33 provincias, ciudades y comunidades autónomas, 333 ciudades a nivel de prefectura y 2851 condados y distritos en todo el país.
La empresa es la única de la industria licorera china que posee dos licores famosos y dos marcas consagradas en Yanghe y Shuanggou. El vino de Shuanggou, cuyo origen se remonta a hace 18 millones de años en la zona de Shuanggou Xia Caowan, se considera el comienzo del vino chino. Sus tres bases de producción (Yanghe, Shuanggou y Siyang) tienen una superficie total de más de 10 kilómetros cuadrados, más de 1000 equipos de vinicultores, más de 70 000 bodegas de vino y una capacidad de producción anual de 160 000 toneladas del famoso vino.
Con una capacidad de almacenamiento de vino de un millón de toneladas, Yanghe es la empresa líder con una mayor producción en la industria del licor Baijiu, la más importante tanto en China como en el mundo. En cuanto a investigación y desarrollo tecnológico, en 2003 consiguió descifrar con éxito la tecnología del equilibrio molecular para la tersura y la suavidad e innovó y lanzó el licor extrasuave, por lo que se la conoce en la industria como la creadora de este tipo de licor.
En 2017, en la clasificación de las 50 principales marcas mundiales de bebidas alcohólicas, Yanghe ocupó el segundo lugar en China y el tercero en el mundo, y pasó oficialmente de los antiguos ocho vinos de China a los nuevos ocho vinos del mundo. En 2019, Yanghe fue elegida como una de las «100 marcas chinas más valiosas» de BrandZ y repitió durante tres años consecutivos ocupando el puesto 48 en la lista; fue seleccionada una vez más como una de las 500 mejores marcas globales, ocupando el puesto 215 en el mundo y subiendo 175 posiciones con respecto al año anterior. Entre las 65 marcas chinas de la lista, Yanghe ocupó el puesto 35; en la Cumbre de Desarrollo de Marcas en China 2018, las acciones de Yanghe ocuparon el primer lugar en cuanto a valor de marca de los productos chinos, con un valor de 63 055 millones de yuanes. En 2020, el valor de la marca ocupó el tercer lugar en la lista de la industria ligera china y el segundo en la industria del licor; y fue preseleccionada en la lista de los 100 principales valores de marca de las empresas chinas en 2020, ocupando el puesto 42.

Proyecto integral de digitalización
Los anteriores esfuerzos de digitalización de Yanghe se centraron principalmente en los sistemas de gestión empresarial, incluida su plataforma de ventas, el sistema de planificación de recursos empresariales (ERP), el sistema de gestión de almacenes (WMS) y el sistema de gestión de transporte (TMS). En 2018, Yanghe inició la transformación digital de la fabricación mediante un proyecto integral conocido como el Proyecto de Fábrica Inteligente 5211. El proyecto incluía seis grandes áreas de interés: planificación, producción, calidad, laboratorio, equipamiento y contabilidad de costes.
Los objetivos de Yanghe para el proyecto incluían la estandarización de la producción y el funcionamiento, la visualización de los procesos de producción, la programación inteligente de la producción, el control automatizado de los procesos, una contabilidad ajustada de los costes de producción y la trazabilidad de la calidad.
Yanghe espera que el proyecto permita a su cadena de suministro mejorar la coordinación desde los distribuidores hasta los proveedores de primer nivel, con un flujo de información fluido desde el plan de producción hasta la entrega del producto. El proyecto pretende mejorar todo el proceso de seguimiento y gestión de la calidad mediante la calidad de los materiales de los proveedores, la eficacia de la producción y la reducción de los costes de fabricación y los fallos de los equipos.
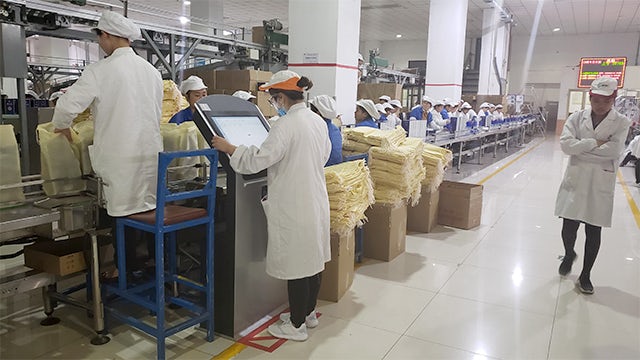
Desafíos técnicos y empresariales
Yanghe cuenta con productos diversos y procesos empresariales complejos. Al investigar el proyecto de digitalización, la empresa identificó más de 100 problemas de planificación, producción, calidad, equipos y finanzas, y más de 40 oportunidades para mejorar la eficiencia y reducir costes.
Un ejemplo de ello es un taller de envasado local que cumple las normativas y procedimientos de inspección a todos los niveles, incluido el control de calidad durante el proceso (IPQC), el control de calidad del producto final (FQC), el control de calidad de salida (OQC) y el muestreo de laboratorio. Uno de los retos era que los datos de las inspecciones se registraban y distribuían en papel, lo que no permitía responder con rapidez a los resultados de las inspecciones ni gestionarlas con eficacia.
Otro ejemplo es el típico proceso de producción de licores basado en el flujo. Cada línea de envasado tiene un proceso de producto correspondiente, y la línea cuenta con un sistema de codificación para la trazabilidad del producto y los servicios de entrada y salida. Como Yanghe utilizaba registros manuales, la gestión de la fábrica carecía de transparencia.
Yanghe también se enfrentaba a un reto técnico: el equipo de producción era muy antiguo, y muchas máquinas no podían recoger datos directamente y no funcionaban bajo controles automatizados. Gran parte de los equipos se estaban transformando para automatizarse. Se aplicaron múltiples sistemas para la cooperación entre equipos, con múltiples interfaces.
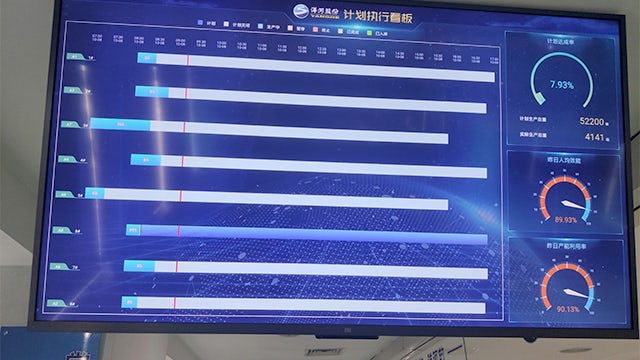
Selección de soluciones de Opcenter
Una vez aprobado el plan de Yanghe para la fábrica digital, la empresa evaluó a varios proveedores de soluciones en China y en el extranjero. Las soluciones de Siemens Opcenter™ satisfacían la estructura global del sistema, y finalmente se confirmó el acuerdo de cooperación entre Yanghe, Shanghai Huicheng, socio comercial de Siemens, y Siemens.
La elección de las soluciones de Siemens obedeció a varias razones. En primer lugar, Siemens ofreció un sistema de ejecución de fabricación (MES), el software Opcenter Execution Process, adaptado a las industrias de procesos. Siemens también ofreció Opcenter Scheduling, que cumplía con los requisitos de Yanghe para la programación inteligente de la producción. El portfolio de soluciones de Siemens también incluía un sistema de gestión de información de laboratorio (LIMS), Opcenter Laboratory, que Yanghe podía aprovechar para integrar a los proveedores y optimizar la recopilación, el análisis y la generación de informes de datos de calidad en laboratorios y líneas de producción. La combinación de MES, APS y LIMS integrados en una plataforma colaborativa podría ayudar a Yanghe a mejorar la precisión contable, proporcionar el estado de producción de cada unidad de negocio y mejorar sustancialmente la eficiencia operativa y de producción, así como aumentar la calidad del producto.
Con una amplia base de clientes en las industrias de alimentación y bebidas y de procesos, así como funcionalidades de soluciones específicas para cada industria, Siemens evidencia su profundo conocimiento de los requisitos de los usuarios, sus sólidas soluciones orientadas al negocio y su asistencia técnica global.
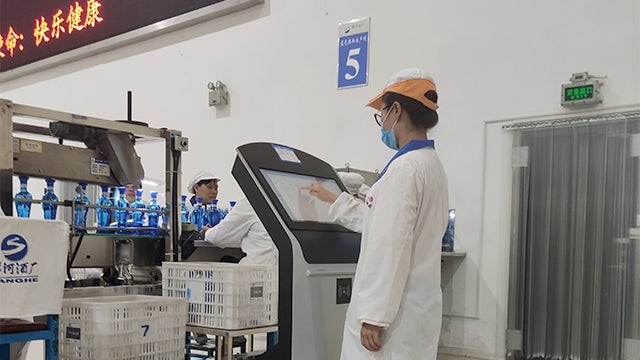
Implementación de la fábrica inteligente
Siemens ayudó al equipo del proyecto a evaluar los requisitos empresariales de Yanghe y colaboró en la planificación y el diseño detallado de la solución global. Basándose en las funcionalidades del software Opcenter y en los requisitos de la empresa, el equipo de implementación del proyecto estableció 13 modelos que abordaban cinco aspectos, como la reparación automática, la predicción en tiempo real, la toma de decisiones autónoma, el análisis de modelos y el análisis de correlación, para mejorar en gran medida el control inteligente de la producción.
Para implementar el proyecto de fábrica inteligente, Yanghe sustituyó un proceso de programación basado en hojas de cálculo por el software Opcenter APS. Integrando las funcionalidades del software con los procesos empresariales de Yanghe, el equipo del proyecto desarrolló reglas para programar los materiales y equipos necesarios, minimizando al mismo tiempo los tiempos totales de preparación de la producción. Yanghe también definió indicadores clave de rendimiento (KPIs) y sus requisitos de información.
La implementación de Opcenter Execution Process en Yanghe aportó mejoras evidentes gracias a la sustitución de las operaciones humanas por el control automatizado mediante software y a los dispositivos y datos integrados, que recogen las cantidades de producción y las velocidades de funcionamiento de cada proceso a través de instrumentos y equipos automatizados.
Para los procesos de inspección de calidad, Yanghe implementó las funcionalidades de Opcenter Laboratory para la inspección IQC, la gestión de códigos de barras, el escaneo automático y la inspección OQC con el fin de crear un sistema de recopilación de información de calidad y una plataforma de gestión de calidad, así como para realizar la trazabilidad de la calidad en todo el proceso, desde los productos acabados y semiacabados hasta las materias primas.
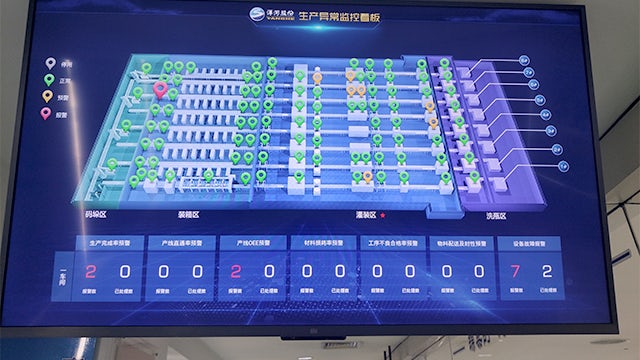