A leading global supplier of electrical connections optimizes processes with PLM
Wago uses NX and Teamcenter to sharpen its competitive edge.
Wago Kontakttechnik
Wago Kontakttechnik GmbH & Co. KG develops and manufactures innovative components for electrical connections and automation devices.
http://www.wago.com- Headquarters:
- Minden, Germany
- Products:
- NX, Teamcenter
- Industry Sector:
- Electronics, Semiconductor devices
Regarding the CAD/PDM selection process, we looked particularly at the possibility of automating our complete process chain…from the design of our products, to manufacturing equipment and mold design, to manufacturing. We made the decision to select software from Siemens Digital Industries Software, and we have had very good experiences as a result of our decision.
Wago Kontakttechnik
A leader in spring-based electrical connections
Founded in 1951, Wago Kontakttechnik GmbH & Co. KG (Wago) was dedicated to replacing the normal screw-type electrical connectors with a safer alternative. The basis for this was a patent the young company owned for a spring pressure clamp. Although, at first, material quality problems complicated production of spring pressure clamps, the company eventually transformed this product into a major success.
Today, spring clamp technology is a worldwide industry standard and Wago is one of the global market leaders in spring-based electrical connections. This technology offers many advantages over conventional screw-type clamps. It is easier to assemble and disassemble, does not require maintenance and prevents failures caused by heat or vibration. Products from Wago contribute to safe and reliable operations of machines and facilities around the world.
Worldwide activities
This third-generation, family-owned company today has more than 5,800 employees, 1,800 of whom work at its headquarters in Minden, with another 1,000 at its second German development and production site in Sondershausen. Two more development and production sites are located in Switzerland and China, with additional manufacturing sites in France, India, Japan, Poland and the United States. With 22 subsidiaries and sales networks in 30 countries, the company runs two business units: electrical interconnections and automation.
Wago’s components for electrical connections are based on the maintenance-free spring clamp technology. Because of their reliability, these products are optimally suited for use in energy and building technology, automotive production, traffic and process engineering, as well as plant construction and engineering.
These modular devices can be adapted flexibly and precisely to several automation tasks. They are used where high performance and safety are absolutely essential, such as in production plant equipment, the process industry, building automation and in safety-relevant or explosion-prone areas.
There are numerous considerations that impact the effective development and manufacture of Wago’s products, including rapidly increasing product diversity; the continuous development of advanced, innovative quality solutions and a highly competitive market; as well as a high level of vertical production for manufacturing equipment and tooling. Furthermore, global operations require flexible development and manufacturing processes. The company decided early-on to support its operations by using advanced information technology (IT) solutions, especially product lifecycle management (PLM) software in the areas of computer-aided design (CAD), computer-aided manufacturing (CAM) and product data management (PDM).
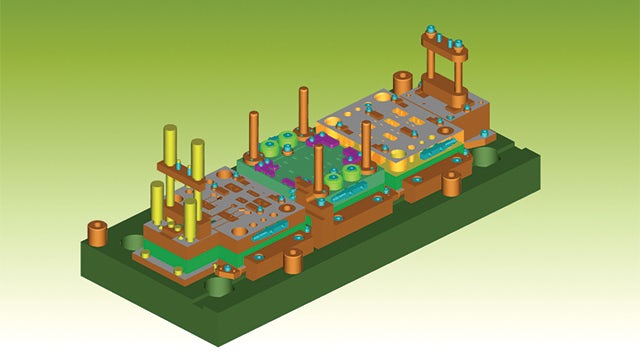
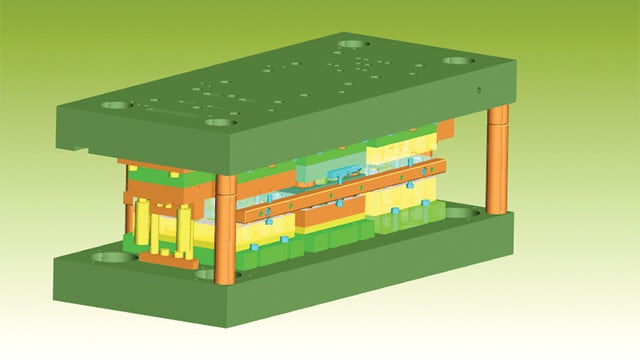
Progressive die design created using NX.
Selecting the right solution
Considering the limitations of Wago’s CAD/CAM software, especially a lack of 3D integration between modules, the company decided to have a detailed look at other solutions.
In 1999, Wago performed a thorough test of three different lifecycle solutions from leading PLM suppliers, choosing NX™ software and Teamcenter® software, both from Siemens Digital Industries Software. The crucial criteria behind this decision included the solution’s highly integrated modules for 3D modeling, numerical control (NC) programming and analysis, as well as a flexible and open architecture.
“Regarding the CAD/PDM selection process, we looked particularly at the possibility of automating our complete process chain... from the design of our products, to manufacturing equipment and mold design, to manufacturing,” says Michael Burmester, head of process and product data management at Wago. “We made the decision to select software from Siemens Digital Industries Software, and we have had very good experiences as a result of our decision.”
In addition to 3D modeling and drawing creation, Wago also uses NX for freeform modeling, the design of injection molds, sheet metal design, advanced assembly design, visualization and rendering, kinematic analysis, user-defined features, and NC programming. In addition, Wago is using NX Wave™ feature functionality and software from Bihler.
NX Wave enables a structured approach for product conception and design and allows users to define and control geometric dependencies of components across assemblies. This is an especially big advantage when complex products are designed and changed by design teams and in the design of product variants.
The software from machine tool manufacturer Bihler supports the integrated design of tools that are used to manufacture the Wago spring clamps on Bihler’s automatic bending machines. All product data and information required for development and manufacturing is shared between the distributed design and production sites using Teamcenter. This enables tooling to be modified and optimized at another site.
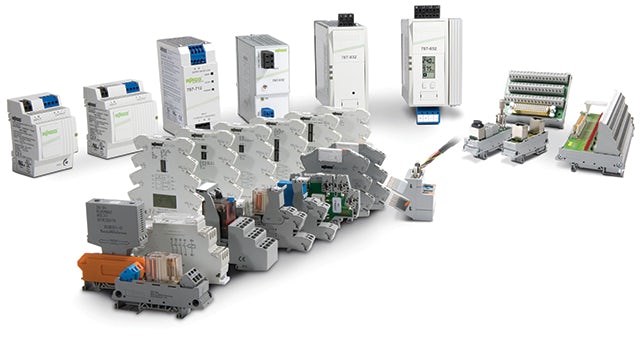
An interface solution for all applications
PLM as foundation for a comprehensive strategy
With the PLM solution fully deployed, including the transfer of existing design and manufacturing data into the system, Wago decided to extend the capabilities of its already highly productive PLM environment. The new, multi-stage project began in 2008 after an 18-month planning phase.
Completed in 2012, enhancements included linking Teamcenter with Wago’s internal enterprise resource planning (ERP) system, expanding the use of Teamcenter to include process and project management functionality, and managing more product-related data and documents. Moreover, all Wago products that require certification issued by national or international agencies and organizations – such as Physikalisch-Technische Bundesanstalt (PTB) in Germany and Underwriters Laboratories (UL) in the United States – are now managed using Teamcenter. More than 130,000 compliance datasets and numerous Wago patents are managed with Teamcenter.
“We want to describe the complete lifecycle of our products, including revisions,” says Burmester. “In addition to the product engineering process, we are also going to implement the product optimization process, which is very important to us. For instance, in 2010 we introduced a new cage clamp that has the same capacity as its forerunner, but is 50 percent smaller. When we replace our internal ERP solution with SAP, we will automatically distribute all relevant product data, documents, and change orders from Teamcenter to SAP. This is another step towards optimizing the process chain and minimizing administrative efforts. We expect similar results from the replacement of five different management systems by using Teamcenter in our automation division.”
Already, Teamcenter is used in areas outside product development, including the information systems technology used in purchasing, quality assurance and production.
“For visualizing 3D product models, we generally use the JT data format and JT viewer in all departments outside product development,” says Burmester. “This allows all authorized employees in different departments to view, inspect and measure 3D models.”

Integrated engineering workplace (solutions of Siemens Digital Industries Software, SAP and Microsoft).
More integration, greater efficiency
Burmester notes that while much has been achieved, much remains to be done. Among the most important projects in process is the implementation of SAP® Business Suite applications for production control and the integration of SAP with Teamcenter. Wago plans to accomplish the latter by using the Teamcenter Gateway for SAP Business Suite from Tesis, a long-time partner of Siemens Digital Industries Software. With SAP deployed and integrated with Teamcenter, the company expects to have achieved another milestone: the elimination of a number of disparate systems and a substantial reduction in administrative effort.
Burmester’s team is also developing an online product configurator that will enable customers to configure and order Wago products online. The combination of Teamcenter and SAP will make it possible to automatically send configured products to production for immediate manufacture.
Additional PLM projects include unifying different computer-aided engineering (CAE) systems for analysis and simulation, and a requirements management solution.
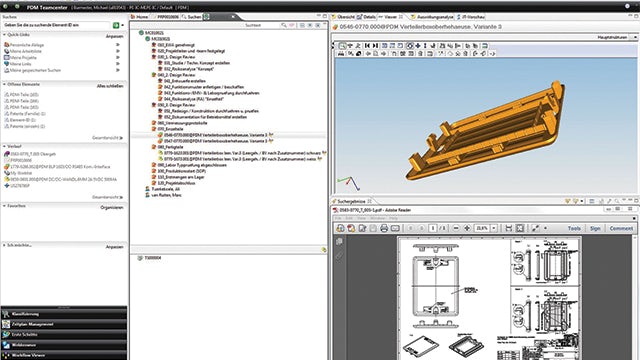
Product-engineering projects managed with Teamcenter.
Quantifying success
Burmester says that while it’s not easy to quantify the success that Wago has achieved with these IT projects, especially considering dynamic company growth and a rapidly changing market environment, he points out: “What we can say is that our product range has more than doubled in the last ten years, and being able to handle that with approximately the same number of people is a huge benefit. Without the integrated CAD/CAM/PDM software systems, the work could not be done at all. There are now more than twice the number of products and related product information, because 3D models, drawings, NC programs, visualization data, and compliance records have increased dramatically.”
Burmester concludes, “We have achieved our current status through improved processes and advanced PLM tools. With fewer interfaces to manage, due to the openness and architecture of NX and Teamcenter, we have been able to keep the administrative effort of all involved parties as low as possible. The combination of NX and Teamcenter has enabled us to significantly shorten our product engineering turnaround, as well as to conspicuously improve our change and optimization processes. The result is that we can react faster to customer requirements, and deliver innovative, high-value solutions in a shorter time.”
The combination of NX and Teamcenter has enabled us to significantly shorten our product engineering turnaround, as well as to conspicuously improve our change and optimization processes. The result is that we can react faster to customer requirements, and deliver innovative, high-value solutions in a shorter time.
Wago Kontakttechnik