Railway vehicle manufacturer uses Statistical Energy Analysis software to deliver reliable acoustic predictions
Siemens Digital Industries Software solution enables Siemens Mobility to adhere to concept phase targets
Siemens Mobility
Siemens Mobility, which includes urban mobility solutions, is a major developer and producer of metros, coaches and light rail vehicles. Current projects include metros for Munich, Germany; Warsaw, Poland and Riyadh, Saudi Arabia; intercity coaches for Austria, Czech Republic and the United States, and light rail vehicles for Qatar, Munich and Den Haag, Netherlands.
https://new.siemens.com/global/en/products/mobility.html- Headquarters:
- Vienna, Austria
- Products:
- Simcenter 3D Software, Simcenter Products
- Industry Sector:
- Automotive & transportation
SEA+ is a user friendly, fast tool and Siemens Digital Industries Software provides perfect support.
Siemens Mobility
Increasing importance of noise, vibration and harshness
The railway industry faces a demanding environment because it needs to accommodate the continuously growing number of requirements of regulatory authorities, while reducing development time and costs to meet the highly-customized needs of clients. All this leads to an increased demand for predevelopment using computer simulation and, when possible, parametric simulation models for customization.
As with other transportation industries, the global challenges in the railway business start with striving for energy efficiency. This has led to the push for lightweight design, which is closely linked to reducing emissions and providing excellent comfort, including lower noise emissions and acoustic comfort. Unfortunately, a lightweight design usually deteriorates the general acoustic behavior or absorbability of rail vehicles. The acoustic behavior and noise emissions of new rail vehicles (inside and outside) are always on public display.
The importance of numerical simulation in noise, vibration and harshness (NVH) will likely increase in the coming years, just as it already has in many other technical disciplines, such as static and dynamic calculation, material engineering, running behavior and wheel-rail-contact, fluid dynamics, aerodynamics and crashworthiness.
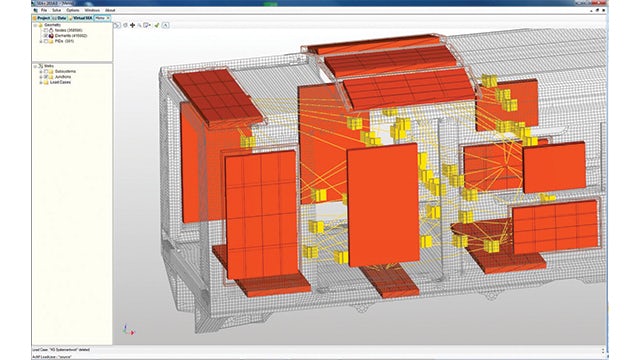
Taking a holistic view with simulation
Siemens Mobility (Siemens), which includes urban mobility solutions, is a major developer and producer of metros, coaches and light-rail vehicles. Current projects include metros for Munich, Germany; Warsaw, Poland and Riyadh, Saudi Arabia; intercity coaches for Austria, Czech Republic and the United States and light-rail vehicles for Qatar, Munich and Den Haag, Netherlands.
The key brand attributes of Siemens rail vehicles are high quality, high-energy efficiency and sustainability. The advantage of Siemens’ rail vehicles is well understood since electric-powered metros and trams are among the world’s most energy-efficient vehicles. To further optimize their products it was crucial to apply simulation in the development process.
The critical NVH issue for Siemens was to comply with the noise regulations of different countries and customers while maintaining low-vehicle weight. That means one size doesn’t fit all: for each project Siemens has to find a noise treatment that fits the customer’s needs.
The main challenge was to predict the sound-pressure level inside and outside of their vehicles with all sources and transmission paths at various train speeds, and optimize the concepts that were already in the early development process.
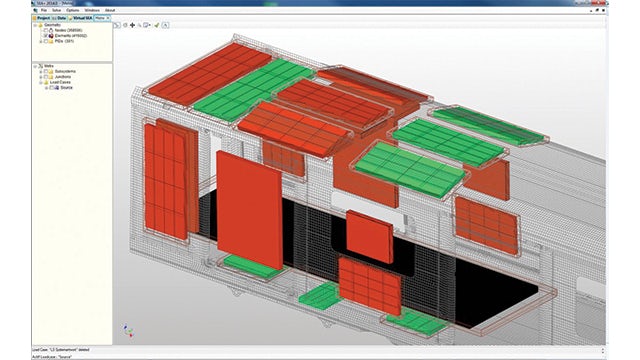
“No longer a black box”
To achieve this goal Siemens used a bundle of Statistical Energy Analysis (SEA+) software from InterAC that is exclusively distributed by Siemens Digital Industries Software. SEA+ is used to complement LMS Virtual.Lab™ software for mid- to high-frequency acoustics and sound-transmission predictions.
The main reason Siemens chose SEA+ was to get a reliable acoustic prediction for a complete rail car, including all sources, components, transmission paths and noise treatments, in an appropriate timeframe with suitable resources for structure and airborne noise. Furthermore, with SEA+ Siemens found it is easy to gain insight into the physical behavior of an acoustic model, which means it is no longer a black box because users are able to follow energy flows and it is possible to understand the physical nature of these flows.
Siemens also uses Virtual SEA (VSEA) software and SEA-Test software. Using VSEA enables Siemens to calculate structureborne transmission paths and other vibro-acoustic parameters, such as mobility, modal density, etc., out of an existing finite element (FE) model created by the structural calculation department. Furthermore, you don’t need a test specimen, which means it is possible to make validations directly with the FE model and build up the SEA+ model on the FE model.
Siemens uses SEA-Test software to analyze test results for validation and input data such as damping.
During the implementation period Siemens was able to get a deep understanding of SEA modeling. The major benefit of having reliable models is they can be used to support the early-concept design for rail vehicles and evaluate changes during the design-to-cost (DTC) and design-to-weight (DTW) processes. Because of physical SEA models it is possible for Siemens to design their vehicles closer to limit values.
Providing state-of-the-art workflow “SEA+ is a user friendly, fast tool and Siemens Digital Industries Software provides perfect support,” says Sebastian Preis, acoustic engineer at Siemens Mobility. “It is the only software suite that combines different simulation approaches and measurements. SEA+ has unique functions. The combination with VSEA opens new options, which to my knowledge is the only one on the market.
“The reason SEA+ is better than our previously installed simulation solution is because it offers a self-explanatory GUI and is very fast in terms of modeling and calculation time. The whole workflow is state-of-the-art and is thought out down to the tiniest detail. It is possible to calculate the vibro-acoustic behavior of a complete rail car in almost the whole frequency range of interest.
“The combination of SEA, virtual SEA and SEA-Test is unique; especially VSEA, which increases accuracy and robustness when there is no available test specimen or time for measurements. SEA+ is a class-leading tool in terms of functionality, usability, workflow and extensions like Virtual SEA, which allows you to have access to an FE model.”
Siemens has used SEA+ for calculating structure-borne and airborne transmission paths, VSEA for coupling-loss factors (CLFs) and the indirect coupling of loss factors for the global modes and SEA-Test to measure damping loss factors (DLFs) and CLFs for components such as doublelayered floors.
“Before we started with NVH simulation the acoustic management in a project was based on a lot of experience, measured data and Excel calculations,” says Preis. “So it was necessary to use a bigger safety margin to limit values than with simulation. Furthermore, with simulation it is possible to handle a project with certitude from the predesign process.
“Another big advantage is the ability to easily update a model during the design process and to conduct a delta analysis. During a project we often have questions like this: ‘We want to change the door, does this affect the acoustic inside the rail car?’ To update an SEA+ subsystem of an existing complete model is easy and you get the result in a short time.
“In the end, the major change that SEA+ facilitated was that we were able to start the simulation process for a complete rail car in the very early design phase.
“SEA+ is a very efficient and effective tool to engineer acoustic performance of complete rail vehicles across the relevant frequency range, allowing us to produce vehicles with high comfort in a market environment that demands lighter weight and more cost effectiveness.”
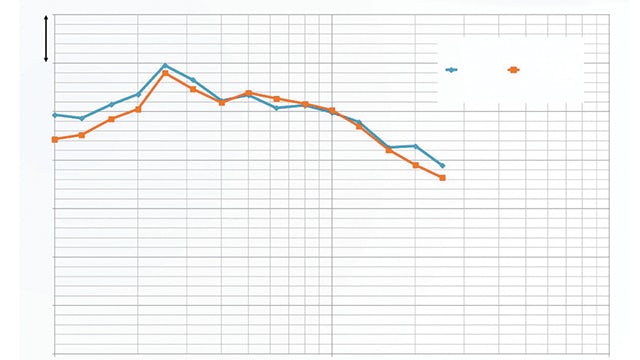
In the end, the major change that SEA+ facilitated was that we were able to start the simulation process for a complete rail car in the very early design phase.
Siemens Mobility