Danfoss’ digital journey and strategic approach to MES
Leveraging Siemens’ industry-leading technology in a flexible enterprise architecture approach
Danfoss
Danfoss is a privately-owned, multinational company headquartered in Nordborg, Denmark. The company’s expansive portfolio of industrial solutions and components includes hydraulics, motors, controllers, drives, compressors, sensors, switches, pumps, and meters that are designed to drive global advancements in sustainability for energy efficiency, renewables, food supply, and connectivity.
https://www.danfoss.com/en/- Headquarters:
- Nordberg, Denmark
- Products:
- Opcenter Execution
- Industry Sector:
- Industrial machinery
Siemens’ MES allows us to take the best practices from numerous different legacy methods and build them into one templated toolset.
Danfoss
Elevating industry standards
Leading the way to sustainable transformation, Danfoss, a global company headquartered in Denmark, is meeting many of the world’s climate, urbanization and food challenges with proven and reliable solutions. Driven by the power of an electrified society and fueled by the opportunities of going digital, Danfoss is dedicated to engineering solutions that can unleash the potential of tomorrow.
One of the key challenges facing companies today is how to reconcile highly configurable products with high volume and high variation. Danfoss’ competitive advantage is its time-to-market delivery for new products. Danfoss’ products are typically regionalized and personalized for the customer, which requires an increasing number of configurations.
More complex and configurable products increase the complexity at the shop floor level and challenge manufacturing process efficiency. As a result, introducing new products requires an adaption of shop floor processes. Competition challenges the timeto-market paradigm, accelerating the unveiling of more complex products. As a result, manufacturing lines and processes must quickly adopt new configurations and handle a larger mix of products as customers demand more complex and personalized products at a higher quality level.
Realizing these modern challenges, Danfoss is embracing digitalization in all areas of its organization. Danfoss supplies products in different ways, from make to stock, make to order, configure to order and engineer to order. The flexibility of an end-to-end information technology (IT) architecture is vital to Danfoss successfully serving its customers.
For Danfoss, digitalizing its manufacturing operations ensures high quality production with repeatability and data-driven decisions. Digitizing its manufacturing operations requires a lean approach to platforms, while maintaining flexibility for local differences.
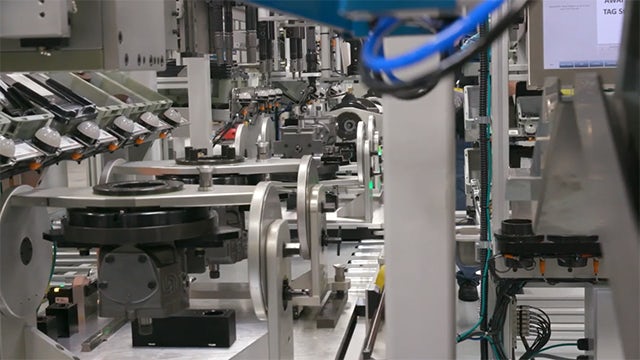
Benefits of Siemens solutions
Danfoss and Siemens Digital Industries Software began working together almost 20 years ago. In 2011, they started a successful collaboration within the manufacturing operations area. Leveraging Siemens’ global presence and industry insight are key benefits of the implementation of Siemens Opcenter™, a holistic manufacturing operations management (MOM) solution that enables companies to implement their strategies for the complete digitalization of manufacturing operations.
As part of its digital transformation, Danfoss is installing the requisite systems to ensure a smooth transition. Customer relationship management (CRM), product lifecycle management (PLM), enterprise resource planning (ERP) and manufacturing execution system (MES) systems all have to work seamlessly together.
Danfoss offers various options to configure specific product models to best suit customer needs. The company vows to increase its product variation and complexity to help customers stay competitive.
“As we add product variation, we can continue to make the system simpler and, in the end, provide better quality at the same or better cost than what we have today,” says Dave Wohlsdorf, senior director of strategic innovation platforms and processes, Danfoss.
“Our systems need to be able to communicate from design through our manufacturing execution systems, to the people working in the assembly or in different manufacturing cells. We need to duplicate what the customer expects to receive no matter the location. It’s really important that whatever we do is scalable for the variation that we want to add and scalable to work in different locations around the world.”
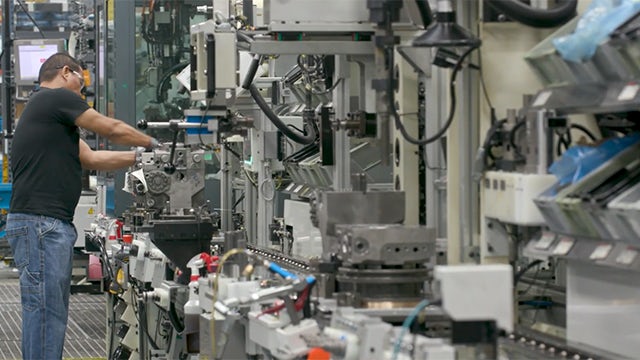
Finding the perfect software tool
Danfoss realized that having a tool to unify the requirements from different sites created a template, making it easier to execute customer requests. That unified tool, Siemens Opcenter, supports a true flexible IT enterprise architecture approach. Being a robust platform with the flexibility to accommodate local needs, Siemens Opcenter is a key enabler for manufacturing operations digitalization and supports Danfoss’ broad product portfolio.
Danfoss regularly uses the International Society of Automation (ISA)95 model. The enterprise layer at layer 4 focuses on product definition and the definition of the production order at a basic level. Layer 3 focuses on execution and all other MOM componentry necessary for execution, and then layer 2 and below focuses on controls systems.
Leveraging its templates, Danfoss more easily handles the integration between the layer 3 MOM solutions up to the enterprise platforms of ERP and Siemens’ Teamcenter® software. The company also has basic templates in place for integration between its Siemens platforms and lower level controls tools.
“From an IT perspective, having a unified tool allows us to unify the requirements from different sites and it makes us much faster in executing because we can come with something that’s already a template,” says Allan Pedersen, IT Senior Director, Engineering and Manufacturing, Danfoss. Siemens’ global services organization, with broad industry insight from design to manufacture, is a major benefit of Danfoss’ partnership with Siemens.
Siemens offers support on all levels, from single resources to a full global team, with the goal of successfully digitizing its processes. Siemens has helped Danfoss implement a robust platform, securing high quality and stable production while increasing productivity and enabling scalable foundation for further growth.
Danfoss uses Opcenter Execution Foundation, Siemens’ Manufacturing Execution System (MES) platform, to ensure a smooth expansion to other facilities without jeopardizing quality and efficiency. Finding the right balance is one of the company’s primary challenges.
“The improvements we’ve realized using Siemens’ MES are largely around time to deployment,” says Pedersen. “Because we have templates of these tools, we walk into a conversation with an existing set of expectations. Instead of talking about all of the different ways something could be done, we’re talking about how to apply the template.”
Pedersen says the company’s transition to using Siemens Opcenter has standardized Danfoss’ manufacturing environment, eliminated much of the guesswork and provided process engineers with a reliable and easily manageable process.
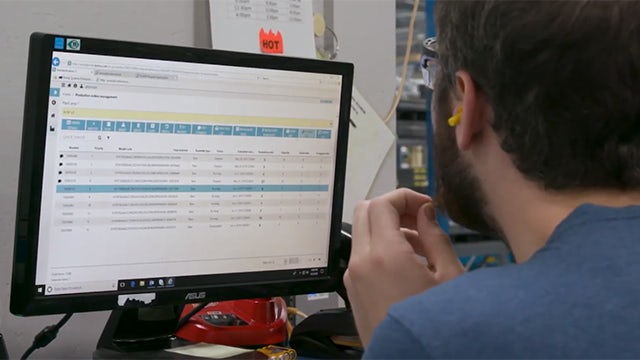
Production execution
Danfoss is a high-volume, high-configurability and high-variation manufacturing company. Siemens’ MES has helped the company’s production process by deploying new configuration to its shop floor, minimizing manual intervention and providing full traceability and product history. Embracing Siemens software has also allowed Danfoss to integrate with shop floor human-machine interface (HMI), support serialization and enjoy flexible management of high product mixes.
“Siemens’ MES allows us to take the best practices from numerous different legacy methods and build them into one templated toolset,” says Pedersen. “This supports us to spread process improvements and eliminate legacy tools. The dual benefit helps improve product quality and process efficiency, while also reducing operational risk and setting the stage for future shared improvements.”
The MES template fulfills several key functions, from ERP and automation integration interface to defect logging, NPI product configuration, reporting, order management, traceability, data recording, management of operator and automation instructions, interlocking.
Siemens’ MES also increases Danfoss’ manufacturing flexibility and efficiently manages a various mix of products. Since deploying Siemens Opcenter, Danfoss has reduced the amount of resources needed to complete a project. With this new solution, the company is much better equipped to handle high-product variation than it was previously. Danfoss can now assure the accuracy of the manufacturing process and possesses the traceability to quickly identify the root cause of any problem.
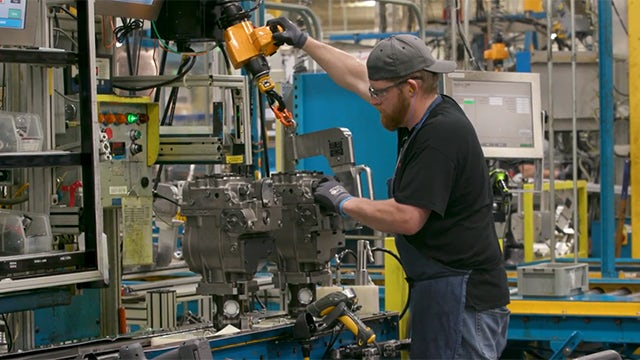
Strategic overview
“Within manufacturing we need to be local while still being global, meaning that we need to be close to where we have facilities to fully understand what is needed,” says Pedersen. “We engage locally and share knowledge globally.”
Global manufacturing companies are experiencing a digital transformation, with enterprise architecture as the key driver. Siemens Opcenter is the catalyst for doing this right.
The long-term partnership around everything from PLM to manufacturing has ensured that Danfoss takes full advantage of Siemens’ industry knowledge. With the assistance of Siemens’ product portfolio, Danfoss has positioned itself to be a major market player today and well into the future.