Tube-processing specialist uses Solid Edge to achieve four-times faster tool programming and expand markets
Addition Manufacturing Technologies, formerly AddisonMcKee and Eaton Leonard, reduces design-tomanufacturing time from 30 minutes to five minutes
Addition Manufacturing Technologies
Addition provides a one-stop solution in the tube-processing sector. The company’s product lines deliver highquality, reliable equipment and precision tooling for tube bending, end-finishing, cutting, notching and muffler assembly.
http://www.additionmt.com- Headquarters:
- Lebanon, Ohio, United States
- Products:
- Solid Edge
- Industry Sector:
- Industrial machinery
Before CAMWorks, it would take 45 to 60 minutes to program our internal Doosan mill turning machine to manufacture a part. With CAMWorks for Solid Edge, this dropped to 15 minutes.
Addition Manufacturing Technologies
Expanding global markets
Addition combined its engineering and production capabilities to expand its global tube-processing markets. It provides a one-stop solution in the tube-processing sector. The company’s product lines deliver high-quality, reliable equipment and precision tooling for tube bending, end-finishing, cutting, notching and muffler assembly.
Addition also offers cell automation solutions, maintenance and service agreements, tool stocking agreements, equipment rebuild/refurbishment, and trade-in programs. Its services include prototyping and part development, training and other educational opportunities.
Engineering software plays a key role in the company’s success and growth. The company employs software, design and manufacturing engineers in the United States, Canada, Mexico and Great Britain.
Transition from 2D to 3D design
In the late 1990s, Addition moved from 2D AutoCAD® software for design to Autodesk® Mechanical Desktop, a 3D CAD product. But the company wanted a more modern, easy-to-use and innovative 3D design tool. In 2005, the company selected Solid Edge® software from product lifecycle management (PLM) specialist Siemens Digital Industries Software.
“The changes from 2D to 3D were made for a lot of the same reasons other CAD users moved,” notes Lonnie McGrew, Tooling Division Vice President, Addition Manufacturing Technologies. “We wanted to model our products, not just draw them. Furthermore, we wanted to be able to check the interferences of the complex and interdependent parts we design. Large assembly design capabilities were needed as well, something our first 3D CAD system lacked. With 3D, we have better visualization for part programming and manufacturing. Using 3D also enhances our ability to review complex tool design with our customers. This is important in particular for tube-bending configurations, which are 3D by nature.”
Two different design groups use Solid Edge currently. The company has 30 seats of Solid Edge globally.
The first group uses Solid Edge to design tube-manipulation machines. Those include tube-bending, end-forming, muffler assembly and hydraulic press machines.
A second group designs the tooling that integrates with the tube-bending, endforming and muffler-making machinery. These complex tooling designs fit on Addition machines as well as the products of other manufacturers. These tools are routinely updated to accommodate new model-year design changes in the automotive market.
“Our tool designers also use Solid Edge XpresRoute for modeling tubes,” says McGrew. “We import tube models from customer data or construct new tube models using XpresRoute from the XYZ data received from our customer. We then use the 3D model of the tube in the design of our tooling. For example, we may need to grip one bend in a tube in order to make the next bend, or grip a bend to perform an operation on the end of a tube.”
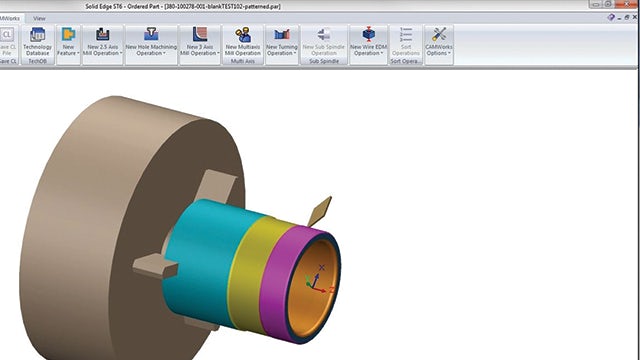
Simulation of the machining process using CAMWorks for Solid Edge.
Solid Edge manufacturing
“Although programmers at Addition have been using 3D since the 1990s, more recently the move to leverage Solid Edge designs for computer-aided manufacturing (CAM) led to the search for a better solution.” says Matt Haines, General Manager of Operations at Addition Manufacturing Technologies.
Haines, who started his career as a machinist on the shop floor and later held manufacturing, engineering and information technology (IT) management positions, recognized an embedded CAM application would shorten the company’s design-to-manufacturing cycle.
Addition turned to CAMWorks® for Solid Edge, an embedded CAM program (developed by Geometric Americas Inc.) that is fully integrated with Solid Edge.
“Adding CAMWorks for Solid Edge gets our designs into manufacturing faster,” Haines says. “We’re an engineering-to-order business with short lead times and must work with limited technical information from the customer. Engineering will design the product to the customer specs and we have a two- to four-week window to get it through manufacturing.
“Before CAMWorks, it would take 45 to 60 minutes to program our internal Doosan mill turning machine to manufacture a part. With CAMWorks for Solid Edge, this dropped to 15 minutes. Put another way, the 70 percent time savings on this process enables the programmers to work on other products; therefore, we achieve similar results because CAMWorks sits inside Solid Edge.”
Addition uses other computer numerical control (CNC) machine brands, including Haas, Hurco, Toyota, Mazak and Mori Sieki, to manufacture parts for customers.
The company uses Solid Edge and CAMWorks application programming interfaces (APIs) to further streamline the design and programming process. For example, “A wiper tip (a perishable bending tool) that previously took 30 minutes, now just takes five minutes using Visual Basic to drive the creation of models and drafts,” says McGrew.
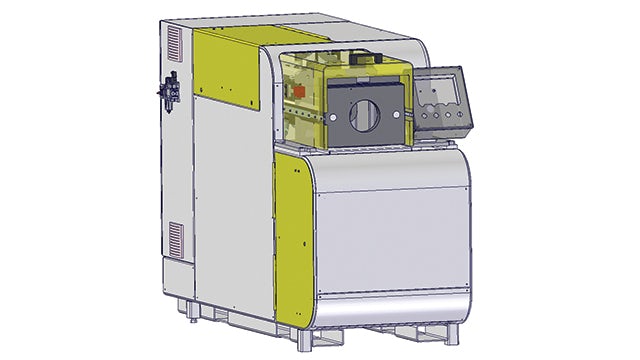
This single-head sizing machine is designed to provide improved accuracy and control of both inside and outside diameters of a tube. This machine uses tooling that incorporates inside expanding fingers and outside reducing jaws in a barrel assembly.
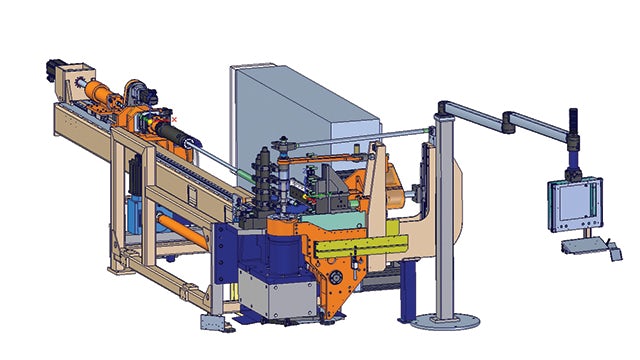
Acclaimed globally for its high quality, this electric CNC tube-bending machine is designed to bend complex tube shapes up to 82 millimeters outside diameter.
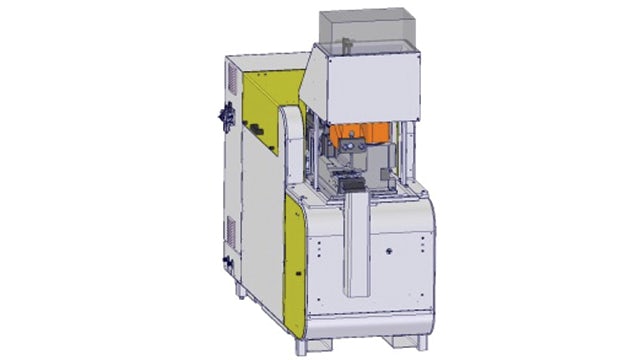
A tube trimming/parting machine is designed for 90 degree parting, anglecut parting, end trimming, radius-cutting, and radius scallop operations on tubes. It uses clamping jaws to hold the tube, while a blade is pushed into the tube to perform the cutting operation.
Solid Edge design management
Addition also uses the Insight™ design data management solution, which utilizes SharePoint® software.
“We use Insight to store all our CAD documents,” says McGrew. “We used to use standard Windows directories to retain CAD information, but we found that we could end up with orphaned assemblies or missing files.
“Along with managing all CAD documents in Insight, additional revision controls will be implemented to make sure all documents are revised with proper authorization.”
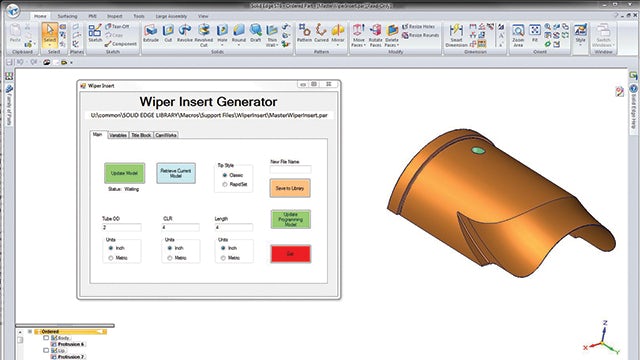
A wiper tip that previously took 30 minutes now just takes five minutes using Visual Basic to drive the creation of models and drafts.
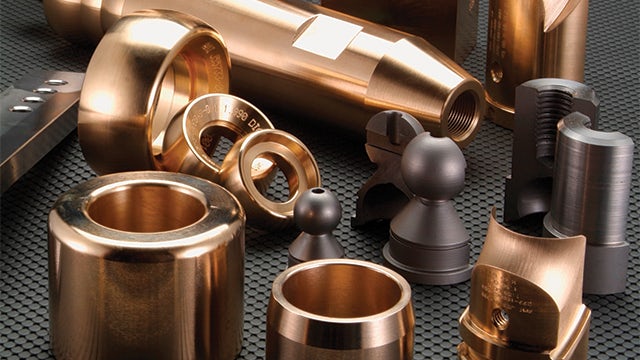
Addition manufactures, in-house, a complete range of perishable bend tools for tube diameters from 25 millimeters up to 200 millimeters to suit a variety of applications and meet its customers’ production needs.
Seeking continuous improvement
The use of Solid Edge with CAMWorks is just one of the ways Addition takes advantage of technology to deliver best-in-class benefits to its customers.
Addition is committed to providing its customers with quality service, solutions and products delivered on-schedule at competitive prices. As a world-class manufacturer, it strives for continuous improvement in products, services and methods in order to obtain complete customer satisfaction.
Adding CAMWorks for Solid Edge gets our designs into manufacturing faster. We’re an engineering-to-order business with short lead times and must work with limited technical information from the customer.
Addition Manufacturing Technologies