Yanghe Distillery verbessert die Produktionseffizienz und -qualität und senkt die Kosten mit APS-, MES- und LIMS-Technologie von Siemens
Opcenter-Lösungen helfen dem weltweit führenden Hersteller von Spirituosen bei der digitalen Transformation
Yanghe Distillery
Yanghe Distillery wurde drei Jahre in Folge in die von Fortune China veröffentlichten „Top 500 Chinese Companies“ aufgenommen und wurde 2012 in den Financial Times Global 500 aufgeführt. Das Unternehmen wurde 2014 und 2015 in die BrandZ™ „Top 100 Most Valuable Chinese Brands“ aufgeführt und belegte 2017 den dritten Platz bei den Brand Finance Spirits 50.
http://www.yangheglobal.com/- Hauptsitz:
- Suqian, Jiangsu, China
- Produkte:
- Opcenter, Laboratory
- Industriezweig:
- Konsumprodukte und Einzelhandel
Weltweit führend bei destillierten Spirituosen
Jiangsu Yanghe Distillery Co., Ltd. (Yanghe) ist in Suqian, der chinesischen Spirituosenhauptstadt, angesiedelt und hat eine Bilanzsumme von 7 Milliarden USD. Yanghe beschäftigt fast 30.000 Mitarbeiter und hat das leistungsstärkste Vertriebsnetz in Chinas Spirituosenbranche aufgebaut. Das Netzwerk verfügt über mehr als 9.000 Direktvertriebe, fast 10.000 Distributoren und 360.000 Gruppen- oder Großeinkaufseinheiten. Es gibt 2 Millionen Point-of-Sale-Partner und direkte Verkaufsstellen in 33 Provinzen, Städten und autonomen Regionen, 333 Städten auf Präfekturebene und 2.851 Landkreisen und Bezirken im ganzen Land.
Das Unternehmen ist das einzige Unternehmen in der chinesischen Spirituosenbranche, das zwei „Chinese Famous Liquors“ und zwei „Chinese Time-honored Brands“ in Yanghe und Shuanggou besitzt. Der Shuanggou-Wein, der vor 18 Millionen Jahren in der Region Shuanggou Xia Caowan entstand, ist der Urquell des chinesischen Weins. Die drei Produktionsstandorte Yanghe, Shuanggou und Siyang verfügen über eine Gesamtfläche von mehr als 10 Quadratkilometern, mehr als 1.000 Winzerteams, über 70.000 Weinkeller und eine jährliche Produktionskapazität von 160.000 Tonnen eines geschätzten Weins.
Mit einer Weinlagerkapazität von 1 Million Tonnen ist Yanghe das führende Unternehmen mit der größten Produktion in der Baijiu-Spirituosenbranche und die Nummer eins in China sowie weltweit. Was die technologische Forschung und Entwicklung anbelangt, so hat das Unternehmen im Jahr 2003 erfolgreich mit molekularer Technologie extra-weiche Spirituosen erfunden und auf den Markt gebracht, wodurch es auch in der Branche Anerkennung erntete.
Im Jahr 2017 belegte Yanghe in der Rangliste der „Top 50 Global Spirits Brand Value“ den zweiten Platz in China und den dritten Platz weltweit und positionierte sich offiziell neu von den alten acht Weinen in China hin zu den neuen acht Weinen für die Welt. Im Jahr 2019 wurde Yanghe zum dritten Mal in Folge von BrandZ in die „Top 100 Most Valuable Chinese Brands“ gewählt und belegte den 48. Platz auf der Liste. Es wurde erneut als eine der 500 besten globalen Marken ausgewählt und belegt weltweit den 215. Platz, was einer Verbesserung um 175 Plätze gegenüber dem Vorjahr bedeutet. Unter den 65 chinesischen Marken auf der Liste belegte Yanghe den 35. Platz. Auf der Informationskonferenz zur Bewertung des chinesischen Markenwerts 2018 belegte die Yanghe-Aktie mit einem Markenwert von 63,055 Milliarden Yuan den ersten Platz im Markenwert chinesischer Produkte. Im Jahr 2020 belegte der Markenwert den dritten Platz in der Liste "2020 China Brand Value" in der Leichtindustrie und den zweiten Platz in der Spirituosenbranche. Außerdem errang er einen Platz auf der Shortlist der „Top 100 Brand Value of Chinese Listed Companies in 2020“ und belegte dort den 42. Platz.
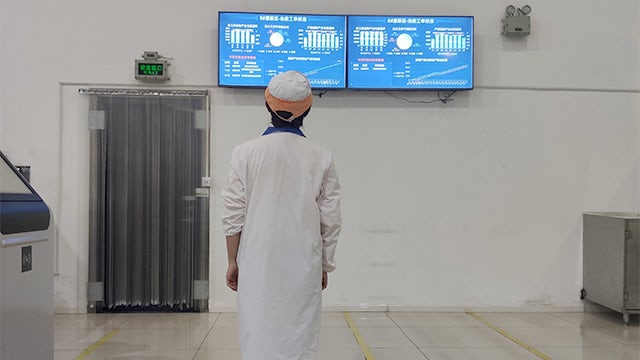
Umfassendes Digitalisierungsprojekt
Die bisherigen Digitalisierungsbemühungen von Yanghe zielten in erster Linie auf Geschäftsmanagementsysteme ab, darunter die Vertriebsplattform, das Enterprise Resource Planning (ERP)-System, das Warehouse Management System (WMS) und das Transportation Management System (TMS). Im Jahr 2018 begann Yanghe mit der digitalen Transformation der Fertigung im Rahmen eines umfassenden Projekts, das als 5211 Smart Factory Project bekannt ist. Das Projekt umfasste sechs Hauptbereiche: Planung, Produktion, Qualität, Labor, Ausrüstung und Kostenrechnung.
Zu den Projektzielen von Yanghe gehörten die Standardisierung von Produktion und Betrieb, die Visualisierung von Produktionsprozessen, eine intelligente Produktionsplanung, eine automatisierte Prozesssteuerung, eine verfeinerte Produktionskostenrechnung und die Rückverfolgbarkeit der Qualität.
Yanghe geht davon aus, dass das Projekt die Lieferkette in die Lage versetzen wird, die Koordination von den Händlern bis zu den First-Level-Zulieferern mit einem nahtlosen Informationsfluss vom Produktionsplan bis zur Produktlieferung zu verbessern. Das Projekt zielt darauf ab, den gesamten Prozess der Qualitätsverfolgung und des Qualitätsmanagements durch bessere Qualität der Zuliefermaterialien, höhere Produktionseffizienz sowie Reduzierung von Herstellungskosten und Anlagenausfällen zu verbessern.
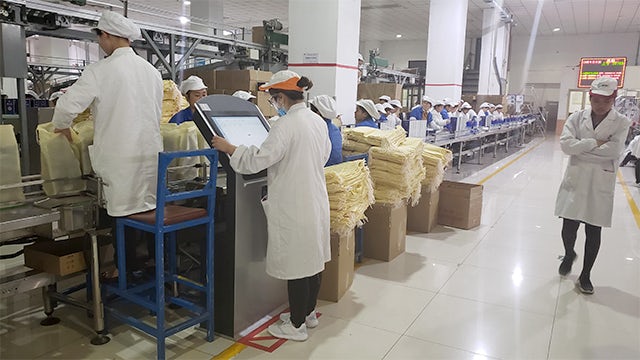
Geschäftliche und technische Herausforderungen
Yanghe verfügt über vielfältige Produkte und komplexe Geschäftsprozesse. Bei der Recherche des Digitalisierungsprojekts identifizierte das Unternehmen mehr als 100 Themen in den Bereichen Planung, Produktion, Qualität, Ausrüstung und Finanzen sowie mehr als 40 Möglichkeiten zur Effizienzsteigerung und Kostensenkung.
Ein Beispiel ist eine Verpackungswerkanlage am Standort, die Inspektionsstandards und -verfahren auf allen Ebenen einhält, einschließlich der prozessbegleitenden Qualitätskontrolle (IPQC), der Qualitätskontrolle des Endprodukts (FQC), der ausgehenden Qualitätskontrolle (OQC) und der Laborprobenahme. Eine der Herausforderungen bestand darin, dass die Inspektionsdaten in Papierform aufgezeichnet und weitergegeben wurden, was eine schnelle Reaktion auf Inspektionsergebnisse und ein effizientes Management unmöglich machten.
Ein weiteres Beispiel ist der typische fließende Prozess der Spirituosenherstellung. Jede Verpackungslinie hat einen entsprechenden Produktprozess und die Linie verfügt über ein Kodierungssystem für die Rückverfolgbarkeit der Produkte sowie für aus- und eingehende Leistungen. Da Yanghe manuelle Aufzeichnungen verwendete, fehlte es der Fabrikleitung an Transparenz.
Yanghe stand auch vor einer technischen Herausforderung: Die Produktionsanlagen waren sehr alt und viele Maschinen konnten nicht direkt Daten sammeln und waren nicht automatisiert. Ein Großteil der Anlagen wurde auf Automatisierung umgestellt. Für die Zusammenarbeit der Anlagen wurden mehrere Systeme mit verschiedenen Schnittstellen eingesetzt.
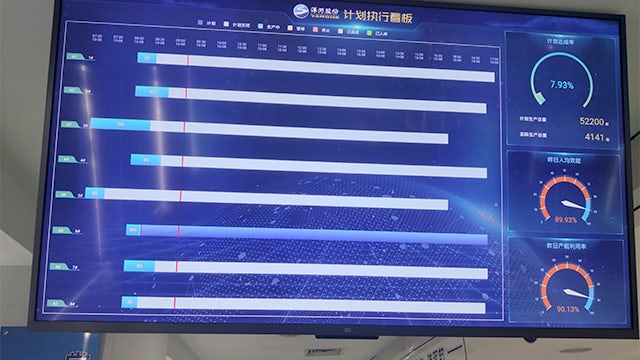
Auswahl der Opcenter-Lösungen
Nachdem der Plan von Yanghe für die digitale Fabrik genehmigt wurde, evaluierte das Unternehmen mehrere Lösungsanbieter in China und im Ausland. Die Opcenter-Lösungen von Siemens erfüllten die gesamte Systemstruktur, und die endgültige Kooperationsvereinbarung wurde nach Abstimmung zwischen Yanghe, Shanghai Huicheng, einem Siemens-Geschäftspartner, und Siemens bestätigt.
Es gab mehrere Gründe für eine Entscheidung zugunsten der Siemens-Lösungen. Zunächst bot Siemens mit Opcenter Execution Process ein Manufacturing Execution System (MES) an, das auf die Prozessindustrie zugeschnitten ist. Siemens bot zudem Opcenter Scheduling an, das die Anforderungen von Yanghe an eine intelligente Produktionsplanung erfüllte. Das Siemens-Lösungsportfolio umfasste auch ein Laborinformationsmanagementsystem (LIMS), Opcenter Laboratory, das Yanghe nutzen konnte, um Zulieferer zu integrieren und die Erfassung, Analyse und Berichterstellung von Qualitätsdaten in Laboren und Produktionslinien zu optimieren. Die Kombination von integriertem MES, APS und LIMS in einer kollaborativen Plattform könnte Yanghe dabei helfen, die Genauigkeit der Buchhaltung zu verbessern, den Produktionsstatus für jede Geschäftseinheit bereitzustellen, die Betriebs- und Produktionseffizienz erheblich zu optimieren und gleichzeitig die Produktqualität zu erhöhen.
Mit einem großen Kundenstamm in der Lebensmittel- und Getränkebranche sowie in der Prozessindustrie und mit branchenspezifischen Lösungskompetenzen stellt Siemens sein tiefes Verständnis für die Anforderungen der Anwender, seine soliden geschäftsorientierten Lösungen und seinen globalen technischen Support unter Beweis.
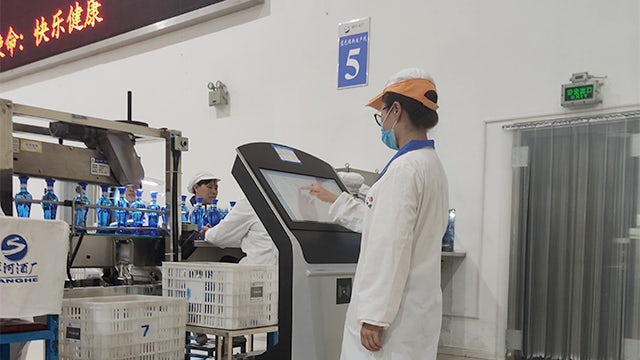
Implementierung der intelligenten Fabrik
Siemens unterstützte das Projektteam bei der Bewertung der Geschäftsanforderungen von Yanghe und half bei der Planung und dem detaillierten Entwurf der Gesamtlösung. Basierend auf den Funktionen der Opcenter-Software und den geschäftlichen Anforderungen hat das Projektimplementierungsteam 13 Modelle entwickelt, die die fünf Aspekte automatische Reparatur, Echtzeitvorhersage, autonome Entscheidungsfindung, Modellanalyse und Korrelationsanalyse abdecken, um die intelligente Produktionssteuerung erheblich zu verbessern.
Zur Umsetzung des Smart Factory-Projekts ersetzte Yanghe einen Planungsprozess, der auf Tabellenkalkulationen basierte, durch die Software Opcenter APS. Durch Integration der Softwarefunktionen in die Geschäftsprozesse von Yanghe entwickelte das Projektteam Regeln für die Planung der erforderlichen Materialien und Anlagen und konnte die Gesamtrüstzeiten für die Produktion minimieren. Yanghe definierte auch Key Performance Indicators (KPIs) und Anforderungen für diesbezügliche Berichterstellung.
Die Implementierung von Opcenter Execution Process bei Yanghe brachte deutliche Verbesserungen durch den Ersatz menschlicher Tätigkeiten durch automatisierte Softwarekontrolle und durch integrierte Geräte und Daten, die Produktionsmengen und Arbeitsgeschwindigkeiten jedes Prozesses durch automatisierte Instrumente und Anlagen erfassen.
Für die Qualitätskontrolle implementierte Yanghe Funktionen von Opcenter Laboratory für die IQC-Inspektion, die Barcode-Verwaltung, das automatische Scannen und die OQC-Inspektion, um ein System zur Erfassung von Qualitätsinformationen und eine Plattform für das Qualitätsmanagement aufzubauen. Zudem sollte die Rückverfolgbarkeit der Qualität des gesamten Prozesses von den Endprodukten und Halbfertigprodukten bis hin zu den Rohstoffen zu gewährleistet werden.
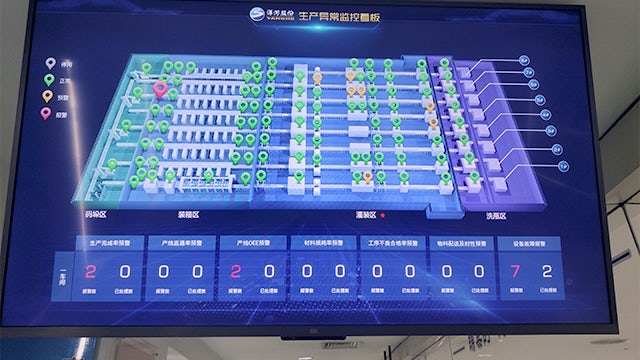